5 Metal Folding Techniques To Know
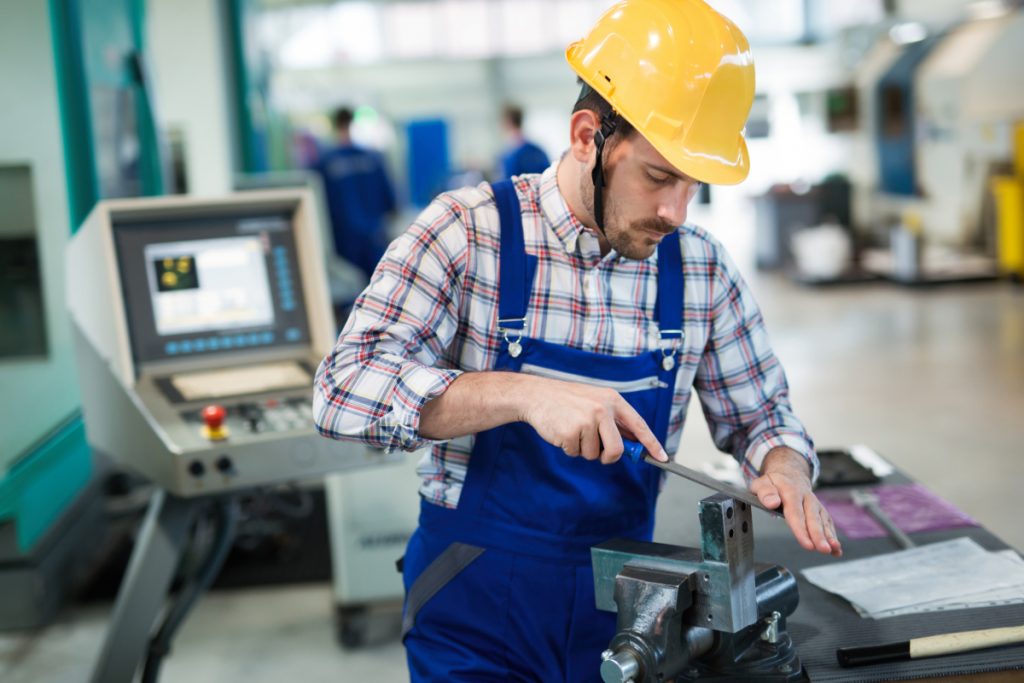
What are some metal folding techniques to know?
- Air Bending
- Bottom Bending
- Coining
- Wiping Die Bending
- Rotary Bending
The process of metal folding is quite straightforward. It involves changing the shape of metal without breaking the material. Specific machines are used to put stress on the metal to manipulate its shape beyond its yield strength but below the limits of its tensile strength. Workers use different types of die-sets to achieve different shapes for the material. Other than that, there are also several metal folding techniques that workers could utilize depending on the project and the resources.
Usually, CNC machines are used for metal folding. Some variations offer more precision and more accuracy, while some others are flexible and good for repeatability. No matter what, each type of metal folding technique has something to offer.
To learn more about these methods for metal folding, keep reading below!
Air Bending
Air bending metal involves a v-opening bottom die and a puncher. When you feed the metal to the press brake, there will be three contact points: the two edges of the v-shaped die and the puncher itself. The angle desired for the metal will be what determines how far the puncher will bend the metal into the die.
This is arguably the most popular and commonly used technique in metal folding. Its notable advantages are its flexibility, meaning you can use a single die for different angles and almost any material. Its low tonnage makes it an even more attractive choice. As you can expect, this technique results in less damage to the material.
Bottom Bending
A similar technique to air bending, bottom bending also uses a v-opening bottom die. However, instead of the puncher pushing down the sheet metal to the right angle, this technique pushes them together completely. The metal will meet the bottom end of the v-opening die, which is how the technique got its name. Thanks to this, bottom bending is known to be more accurate than air bending, and it has less spring back. However, it does require more pressure for the puncher and it needs specific dies for different angles. In other words, you need to change the die used frequently.
Coining
Unlike the first two techniques, coining is a closed die process and it requires high tonnages of pressure. The machine stamps the sheet metal between the punch and the die using high pressure, making it more accurate. This process can be done with a gear-driven press, a mechanical press, or a hydraulic press.
Some advantages of this technique include producing a more detailed and smoother finish as well as, easy repeatability. It also doesn’t require any special equipment to execute. The technique itself already eliminates any additional finishing processes as the grain size will be smaller and the surface will be harder.
Wiping Die Bending
In this process, the piece of sheet metal is held against a die and a wiping flange slides across the part of the metal that protrudes from the pad and die.
This technique, also called edge bending, would push the sheet metal against the edge of the die, bending it to the angle that you need. The flange is held and controlled by an upper shoe and the die is supported by a lower shoe. You can change this up if you want to change the angle of the bend. A spring between the pad and the upper shoe holds the metal before it makes contact with the flange, and it also helps with holding it down as it is being bent.
Depending on the modifications that you make on both the flange and the die, you can decide the angle at which the sheet metal must be bent. Even more, changes could even let you use this technique to fabricate bends.
Rotary Bending
Most commonly used on pipes, rotary bending involves bending the material on a fixed die set to reach almost any angle needed. It is also used for large or heavy sheets that might lead to excess labor and even some safety concerns.
The reason why people use this technique is that it is very flexible and it can even bend metals farther than 90 degrees, with some even reaching 180 degrees. It is also considered a cost-effective technique because it uses over 50% less tonnage and it lessens labor costs.
Key Takeaway
These metal folding techniques have their niches in the metal fabrication industry. If you want to focus on repeatability, you can use coining. If not, you can use other methods that fit what you need for your project.
A good metal folding technique would also need high-quality metals to yield solid results. For this, Metal Exponents can assist you. We supply the finest steel in Asia to our clients from our partners abroad. If you’re interested, you can take a look at our products here, or you can reach out to us here!