Impacts of Unreliable Construction Suppliers
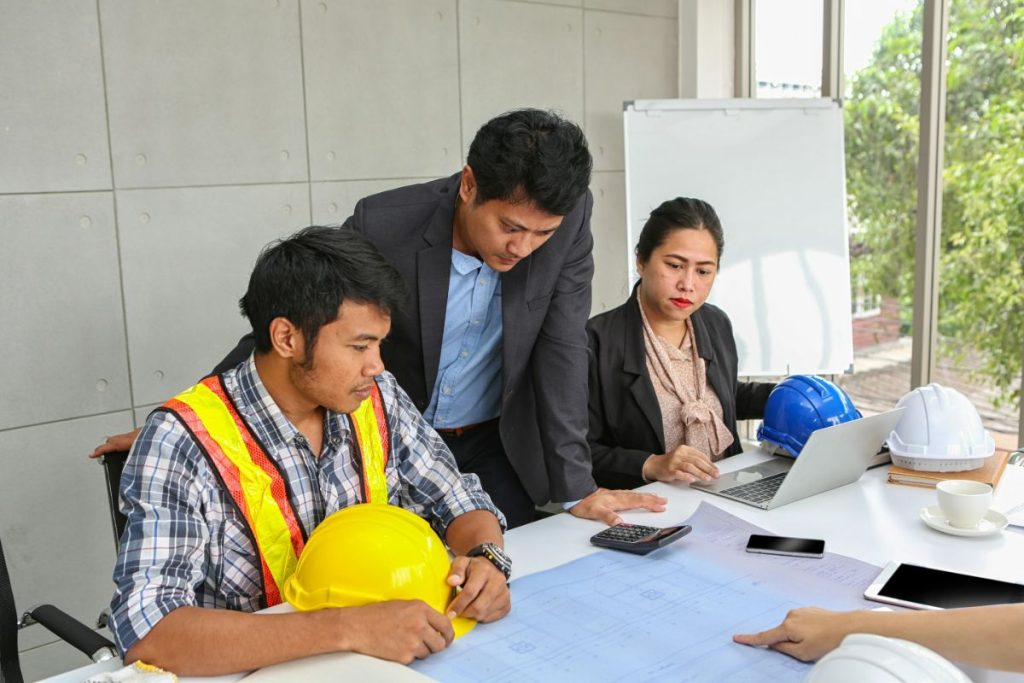
What are the impacts of unreliable construction suppliers?
- Project delays
- Increased costs
- Budget overruns
- Compromised quality
- Legal and contractual risks
Overview
- Partnering with unreliable construction suppliers can lead to significant project setbacks, primarily causing delays when materials are delivered late or fail to meet quality standards.
- Such inefficiencies frequently result in increased costs and budget overruns, as projects incur additional expenses for prolonged labor and unforeseen needs.
- Relying on subpar materials can also compromise the overall quality and safety of the construction, potentially leading to legal complications and hindering project success.
Construction projects rely on dependable suppliers to stay on time, within budget, and up to standard. When suppliers fall short, projects can suffer delays, safety issues, and increased costs.
Therefore, understanding the impacts of unreliable construction suppliers is crucial for project owners and contractors. This article explores the consequences of working with unreliable suppliers and why choosing the right partners is essential to your project’s success. Read on to learn more.
Project Delays
Unreliable suppliers can severely disrupt construction timelines. When materials arrive late, incomplete, or below standard, work may halt while teams wait for replacements or re-inspections. These interruptions result in costly downtime and require rescheduling of labor, equipment, and other dependent tasks.
Logistical challenges such as limited storage, traffic congestion, and unpredictable weather often worsen the impact of late deliveries. When suppliers lack coordination and responsiveness, even minor setbacks can escalate into significant project delays.
To avoid these issues, Metal Exponents Inc. maintains a robust global supply chain and a well-coordinated local logistics system. Our partnerships with reputable steel manufacturers across Asia and Europe, supported by strategic warehousing and reliable transport, ensure materials are delivered promptly and consistently, keeping your project moving forward.
Increased Costs
Delays caused by unreliable suppliers often lead to rising project expenses. Extended labor hours, prolonged equipment rentals, and additional administrative overhead accumulate as construction waits for needed materials. Moreover, firms may face higher costs when rushing shipments or turning to alternative suppliers on short notice.
In the Philippines, these financial impacts are significant, with construction projects reportedly spending 15 to 35 % more due to delays, compounded by challenges like bureaucratic red tape and corruption. Such cost overruns put pressure on budgets and diminish overall profitability.
Metal Exponents Inc. can provide competitive pricing without sacrificing quality by maintaining strong partnerships with trusted international steel manufacturers. Our broad product range also enables contractors to select materials that fit project specifications.
Budget Overruns
Budget overruns are often the result of compounded financial pressures caused by delays and unforeseen expenses. When suppliers fail to deliver materials on time or provide substandard products, contractors must allocate additional funds for rework, material replacements, and penalty fees to cover extended project management and financing costs. These unplanned expenses frequently push total project costs beyond the original budget.
The public sector’s overrun budget is a persistent challenge, leading to project funding delays, resource reallocations, and in some cases, suspension or cancellation of works. Supplier inefficiencies, such as late deliveries and poor material quality, are common contributing factors that jeopardize project viability.
Proactive supplier management and early risk identification are essential to prevent budget overruns.
Compromised Quality
Using unreliable or substandard construction supplies can seriously affect the quality and safety of a finished building. Faulty materials often cause problems such as water leaks, cracks, and early deterioration. These issues weaken the structural integrity and shorten the lifespan of the construction, creating risks for both workers and future occupants.
Quality problems also lead to costly repairs, increased maintenance, and potential regulatory setbacks. This can further inflate costs and prolong construction timelines, impacting the overall success of the project.
We help mitigate these risks by providing premium-grade steel products that comply with international quality standards. Our rigorous quality control process includes factory inspections and verified certifications from trusted manufacturers, ensuring materials are strong, durable, and safe.
Legal and Contractual Risks
Partnering with unreliable suppliers heightens the risk of legal and contractual complications. When materials arrive late or fail to meet agreed standards, contractors may face breaches of contract that lead to claims, arbitration, or litigation. Such disputes can delay projects further and strain relationships among contractors, suppliers, and clients.
These disputes often require costly arbitration or court proceedings, which add financial burdens and complicate project management. In some cases, unresolved conflicts have even led to project abandonment.
By ensuring clear contracts and working with dependable suppliers, construction projects can minimize legal complications, protect reputations, and maintain smoother project progress.
Key Takeaway
Understanding the impacts of unreliable construction suppliers allows you to anticipate challenges and take proactive steps. Early detection helps minimize delays, control costs, and ensure your project stays on track.
Discover quality construction supplies at Metal Exponents Inc. As a supplier, we offer a comprehensive range of materials to meet the demands of any construction project. Contact us today to explore our inventory and build with confidence.