Understanding the Role of Metal Fabrication in the Automotive Industry
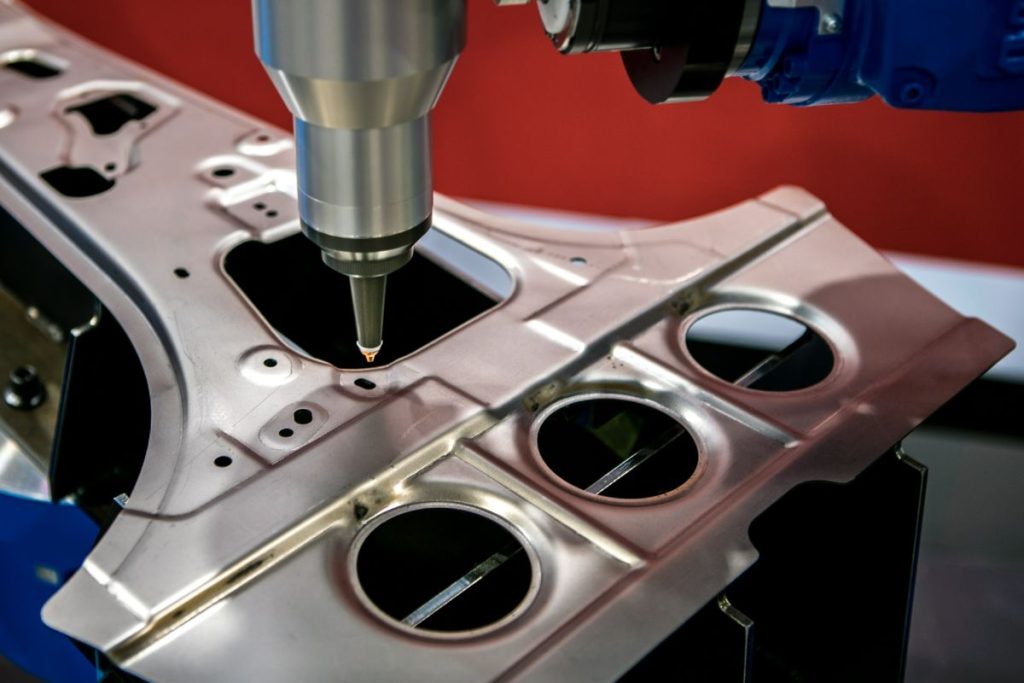
What is the role of metal fabrication in the automotive industry?
- Vehicle frame and structural integrity
- Precision engineering for auto parts
- Custom manufacturing
- Cost-effective mass production
- Sustainability and material advancements
Overview
- This article explores the role of metal fabrication in the automotive industry, including its impact on vehicle frame integrity, precision engineering, custom manufacturing, cost-effective mass production, and sustainability.
- As automotive technology advances, metal fabrication continues to drive innovation, helping manufacturers build stronger, lighter, and more environmentally friendly vehicles.
Metal fabrication is the process of shaping, cutting, and assembling metal to create essential components utilized across various industries like automotive manufacturing. Without precise metal fabrication, vehicles would lack strength and reliability required for everyday use.
In this article, let’s explore the role of metal fabrication in the automotive industry, covering its impact on vehicle construction, precision engineering, cost-effective production, and sustainability. Read on to learn more.
Vehicle Frame and Structural Integrity
A vehicle’s frame is crafted through various metalworking processes, using high-quality materials like steel and aluminum, to ensure strength and support. These components are commonly selected for their balance of durability and weight.
However, the vehicle’s structural integrity depends heavily on the proper fabrication of its metal components. Therefore, improper processing or inadequate quality control can introduce weak points—increasing the risk of bending or breaking under stress.
Fabrication techniques like metal stamping and laser cutting are employed to ensure precise shaping and secure joining of each piece. Furthermore, modern car manufacturers are increasingly utilizing high-strength steel and aluminum alloys, creating light yet stronger frames. This improves fuel efficiency without compromising safety.
Precision Engineering for Auto Parts
Drivers rely on countless metal parts, from engine components to brake systems, that must be engineered with extreme accuracy. Manufacturers achieve this by utilizing advanced cutting, bending, and welding techniques, along with high-techology tools like Computer Numerical Control (CNC) machines and laser cutters.
These machines follow exact measurements to shape metal pieces with minimal error, ensuring a perfect fit every time. Without a precised fabrication, even a small miscalculation could lead to parts that don’t align properly. This affects vehicle performance and safety.
For instance, in engines, precisely machined pistons and cylinders enable smoother movement, reducing wear and tear. Similarly, accurately fabricated brake components ensure proper stopping power, keeping you safe on the road.
By using advanced fabrication techniques and strict quality control, manufacturers help automakers produce vehicles that perform at their best, giving you a smoother and safer driving experience.
Custom Manufacturing
Metal fabricators can create unique components that are not always available in standard production, whether modifying a car for better performance, durability, or aesthetics.
Custom manufacturing is essential for industries like motorsports, where vehicles need specialized frames, suspension systems, or reinforced body panels to handle extreme conditions. It’s also useful for classic car restoration, where original parts may no longer be in production, requiring custom-fabricated replacements to maintain authenticity and function.
Cost-effective Mass Production
Manufacturers can produce large volumes of identical vehicle parts through advanced fabrication techniques like stamping, welding, and CNC machining. This efficiency lowers production costs since automated fabrication reduces the need for manual labor and speeds up assembly lines.
Instead of crafting each car door frame individually, manufacturers use metal stamping to create thousands of identical frames in a fraction of the time, ensuring consistency while keeping costs low.
Another way metal fabrication enhances cost-effectiveness is by optimizing material usage and durability. Automakers use high-strength but lightweight metals, such as aluminum and advanced steel alloys, to create fuel-efficient vehicles without sacrificing safety.
Fabrication processes like laser cutting ensure minimal material waste while maximizing strength. This is particularly important for components like engine mounts or suspension systems, where precision and durability are essential.
Sustainability and Material Advancements
Metal fabrication is crucial in sustainability and material advancements within the automotive industry, as it promotes eco-friendly manufacturing and the use of innovative materials.
Suppliers are continuously seeking ways to reduce their carbon footprint. Steel fabrication supports this by facilitating the recycling and repurposing of metals like aluminum and steel.
Advancements in lightweight and high-strength materials are also made possible through modern metal fabrication techniques. For instance, advanced high-strength steel (AHSS) and aluminum alloys allows car manufacturers to produce lighter yet stronger vehicle components, leading to improved fuel efficiency and lower emissions.
Key Takeaway
The role of metal fabrication in the automotive industry is essential in shaping strong, precise, and efficient vehicle components. At Metal Exponents Inc., we provide high-quality metal fabrication solutions that meet the evolving demands of the automotive industry. Contact us today to learn how our metal fabrication services can support your automotive projects with efficiency and innovation.