Stainless Steel Applications in the Automotive Industry
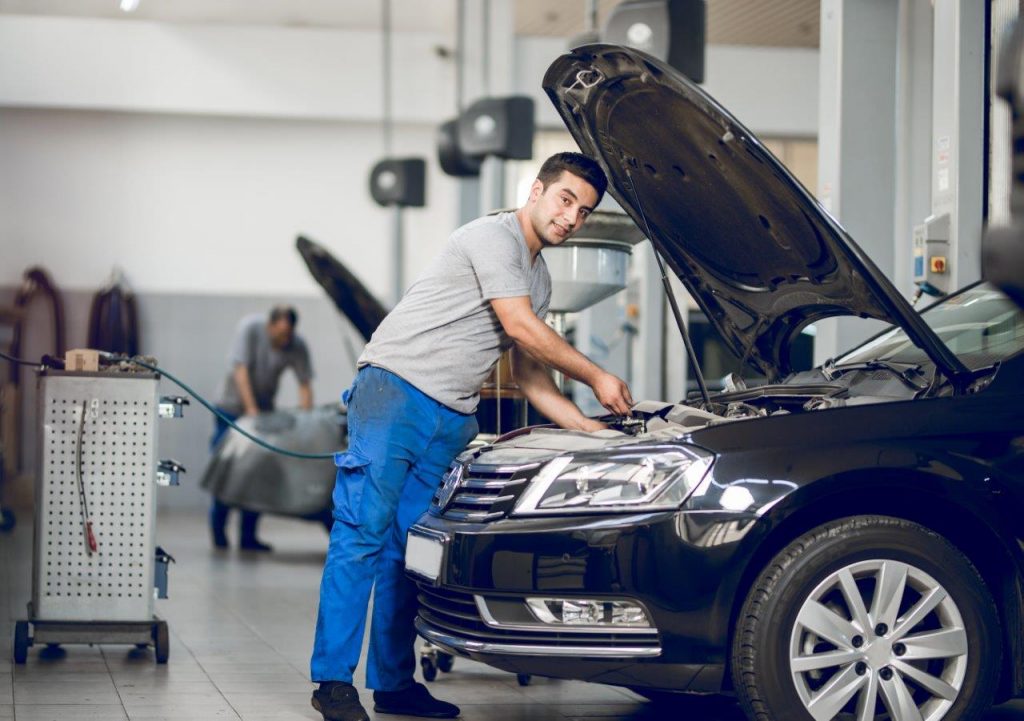
What are the different applications of stainless steel in the automotive industry?
- Exhaust systems
- Tube hydroforming
- Fuel tanks
- Cylinder head gaskets
- Crash test rig for components
Stainless steel is undoubtedly one of the most widely-used materials in the world. It’s lightweight and easily-machined, allowing it to be formed into a variety of dimensions. Though much exploration has been done towards stainless steel applications in automotives, this may have been largely underutilized because of the widespread use of other types of materials.
When it comes to automotive systems, safety and performance are two of the things on the top of the manufacturer’s considerations. Due to a demand to meet these standards, it’s imperative that the properties of stainless steel should be studied to produce high-performing vehicle components. Continue reading to learn more.
Exhaust systems
A vehicle’s exhaust system is important in allowing the vehicle to function for far longer time periods. Basically, the exhaust system is responsible for collecting exhaust gases that are being produced by the cylinders. In this way, harmful substances and other foreign objects which may have been incorporated in the gas will be removed, allowing the vehicle to run more smoothly and reduce discharge as well as the noise level.
Because of the highly-extensive work done by exhaust systems, it’s no surprise that a large part of maintenance costs go towards repairing this hefty-priced component. Keeping this in mind, lightweight and durable materials such as stainless steel make for the perfect choice of parts for manufacturing vehicle exhaust components. Stainless steel can be engineered to resist the effects of destructive conditions experienced by the exhaust engine, enabling car owners to enjoy more mileage on their vehicles.
Through stainless steel, the production of far smaller exhaust pipes has been possible, without compromising the engine performance. This creates an overall lighter, higher-performance vehicle that produces minimal noise.
Tube hydroforming
In line with exhaust systems, stainless steel also makes the best applications for automotives, when it comes to any tube hydroforming-based techniques. One of the main drivers behind this is that this method can be utilized in the production of lightweight vehicle structural components which are lighter in comparison to other kinds of materials.
Simply put, tube hydroforming of stainless steel involves the use of a high or low-pressure form of hydraulic fluid. Inside a mold, an empty, hollow tube is placed inside. The resulting shape is achieved by pumping the fluid into the mold. Using stainless steel, this process is useful in producing vehicle structures like radiator support components, engine cradles, hydraulics, and other suspension parts.
Through stainless steel tube hydroforming, a single stainless steel component can be used in place of multiple individual parts which have all been manually welded into place. This offers vehicles with a higher level of efficiency, especially when it comes to storage space. This also reduces the cost required in making multiple components that can otherwise be done through a single stainless steel tube hydroforming process.
Fuel tanks
As mentioned before, stainless steel has many desirable attributes which make it the smartest choice for virtually almost any kind of automotive application. In particular, its corrosion-resistant properties make it another good choice for automotive fuel tank installations.
Corrosion-resistant fuel tanks are able to withstand different forms of weathering on the material, preventing instances of rust and oxidation which can be costly to repair. This is an important feature to consider knowing that vehicles travel on different surfaces of varying characteristics – foreign materials that may enter the fuel tank will do only minimal harm in distorting this stainless steel-produced component.
Apart from this, stainless steel’s high level of machinability and malleability means that fuel tanks can be shaped in many different kinds of dimensions and sizes, which eventually result in a stronger fuel tank material, as well as a low evaporative emissions capability.
Cylinder head gaskets
Certain manipulative properties of stainless steel make it possible to increase its strength and high fatigue properties. These properties are useful for the production of stainless steel-made cylinder head gaskets which offer a seal between the engine block, as well as the head which covers the cylinders. Gaskets are used for controlled explosions which can result from different combustion processes taking place in the engine – protecting the engine from leakage from internal fluids.
For this specific use, stainless steel requires to be subject to a hardening process, such as cold sheet rolling. As the engine runs, fluctuations in the tensile strength experienced by the head gaskets occur. This repetitive motion requires a significant level of fatigue strength which can be produced using stainless steel.
Crash test rig for components
Stainless steel has also proven to score high on the many attributes which measure a vehicle’s safety capabilities, or “crashworthiness”. This is because stainless steel has resulted in a high absorption capability which even trumps that of commonly-used materials such as carbon, for vehicle frames.
The high absorption capabilities of stainless steel compounded with its ease of manufacturing and high strength make this the perfect crash-testing material in order to gauge a vehicle’s safety in different situations and road scenarios.
Stainless steel offers solutions to some of the most pressing safety concerns that vehicle manufacturers face in their operations, especially when it comes to producing lightweight, fuel-efficient, as well as cost-effective vehicles.
Key Takeaway
In automotives, stainless steel applications include components for exhaust and suspension systems, as well as those for combustion, and for gauging the safety of the vehicle.
There is no other such material that is capable of exhibiting many useful industrial attributes all at once – flexibility, machinability, high-strength, and versatility just to name a few. For vehicle manufacturers, the challenge lies in experimenting on a variety of other uses for this highly sought-after material.