Top Steel Supply Defects that Can Impact Your Project
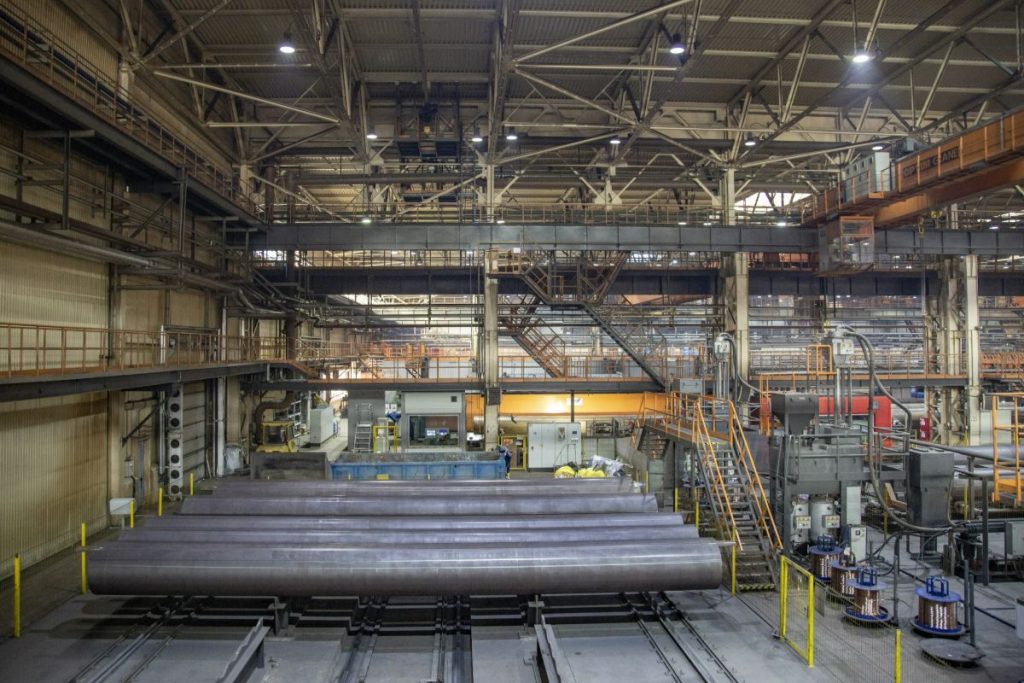
What are the top steel supply defects that can impact your project?
- Warped or bent steel sections
- Surface corrosion and rust
- Inconsistent thickness or dimensions
- Cracks and fractures
- Poor welding and fabrication quality
Overview
- Warped steel and surface corrosion to cracks, inconsistent dimensions, and poor welding; these defects can undermine your build’s integrity and add unexpected expenses to your project.
- Working with a reliable supplier, like Metal Exponents Inc., can ensure your steel supply is defect-free, protecting your construction investment and securing the safety of your structures for years to come.
When you’re managing a construction project, even the smallest defect in your steel supply can lead to major setbacks. From delays and cost overruns to serious structural risks, poor-quality steel compromises not just your timeline but the safety and integrity of your entire build.
That’s why it’s critical to know what to watch out for. Understanding the most common steel supply defects that impact projects helps you catch issues early, ask the right questions, and work only with suppliers who meet the highest quality standards. Read on to learn more.
Warped or Bent Steel Sections
Warped or bent steel sections can cause misalignment during construction, making it difficult to fit the steel components precisely into your design. If your chosen steel has bends or warps, it can affect the integrity of your structure, lead to uneven load distribution, and compromise the stability of beams, columns, or frames.
Lay the steel sections on a flat surface to see if they sit evenly, and use a straight edge or laser level to inspect for bows, twists, or bends along the length of the material. Look from the end of the steel section to spot curves that should not be there.
Surface Corrosion and Rust
Surface corrosion refers to the gradual deterioration of steel’s outer layer, which may look like reddish-brown patches but can lead to deeper damage if left unchecked.
When steel is exposed to moisture, humidity, or salty air without adequate protection, it can develop rust and surface corrosion, weakening the material’s integrity over time.
If you are using structural steel for beams, columns, or trusses, corrosion can reduce their load-bearing capacity, making them more prone to bending or even collapse under pressure.
Many builders choose galvanized steel, which is coated with a layer of zinc to shield it from moisture and oxygen. This protective layer significantly slows down the corrosion process, ensuring your steel components remain strong and durable for years.
Inconsistent Thickness or Dimensions
When steel sections are not uniform, it can lead to uneven weight distribution, misalignment during assembly, and gaps in connections that compromise stability. For example, if you’re constructing beams or columns with steel that has varying thickness, certain sections may not support the intended load.
This can result in increasing the risk of bending, deformation, or even collapse under stress. The inconsistency can also cause delays on-site as your team will need to adjust or replace defective pieces to fit design specifications, leading to additional costs and project downtime.
This defect happens due to poor quality control during the manufacturing process or mishandling during transport and storage. To ensure your chosen steel has the right thickness or dimensions, you can use calipers or micrometers to measure samples upon delivery will help you catch inconsistencies early.
Cracks and Fractures
These often occur when steel cools too quickly during manufacturing, creating internal stresses that lead to cracks as the metal contracts unevenly.
If steel is removed from the heat treatment process and exposed to air without proper cooling control, the rapid temperature change can cause its surface to harden while the inner layers are still expanding.
This results in tiny fractures that may not be visible at first glance, making it crucial to work with suppliers who perform thorough inspections before delivery.
Poor welding and Fabrication Quality
This can happen when suppliers rush production, use inexperienced welders, or fail to follow proper welding procedures and quality checks. You might encounter uneven welds, weak joints, or misaligned connections that compromise the steel’s ability to carry loads or withstand stress.
If you continue to use steel with poor welding and fabrication quality, your project may face serious risks, including joint failures and even safety hazards that can endanger future occupants.
To avoid this, work with a trusted steel supplier that provides proper certifications, quality assurance processes, and transparent documentation for every steel component you order.
Key Takeaway
Understanding how steel supply defects can impact project safety, timelines, and budget is crucial for every contractor, engineer, and business owner in the Philippines. By being aware of these potential defects and addressing them through supplier selection and strict quality checks, you can protect your investment and ensure your structures are safe and durable.
If you want to secure high-quality, defect-free steel for your projects, we are here to help. As one of the Philippines’ most trusted steel suppliers, we provide durable and precisely fabricated steel materials to support your construction needs while ensuring compliance with local and international standards.
Contact us today to experience a hassle-free steel supply process that protects your project from costly defects and delays.