5 Types of Welding Processes
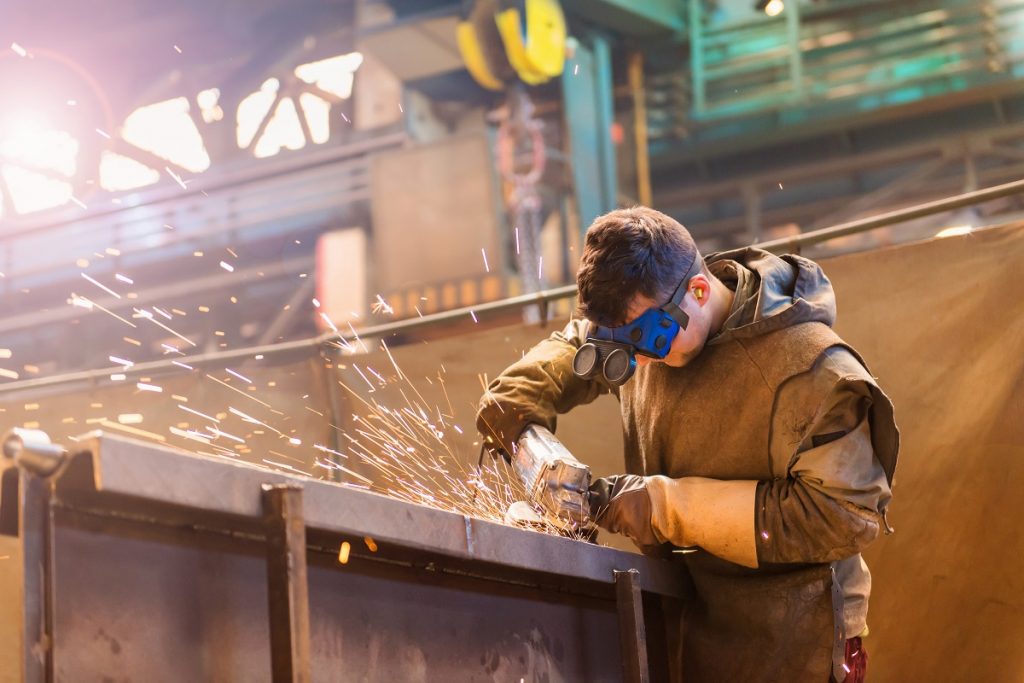
What are the different types of welding processes?
- Gas Tungsten Arc Welding
- Gas Metal Arc Welding
- Flux Cored Arc Welding
- Electron Beam Welding
- Atomic Hydrogen Welding
It’s not always the case that fabricated metal parts are used in standalone applications. Most of the time, they under different types of welding processes, especially if there is a need to combine/fuse two or more metal parts together. This makes the end-product more usable in structural, industrial, or construction applications, compared to its previous form.
Different welding techniques exist, depending on the suitability of the material. For example, the welding process for stainless steel, alloys, or non-ferrous materials may be vastly different from the welding process required to join steel products together. Other parameters such as temperature, pressure, and availability of filler material may also be considered.
Although popular welding processes such as shielded metal arc welding exist, you’ll also encounter Gas Tungsten Arc Welding, Atomic Hydrogen Welding, Flux Cored Arc Welding, and the like. Read on to learn more.
Gas Tungsten Arc Welding
In Gas Tungsten Arc Welding (GTAW) or Tungsten Inert Gas Welding (TIG) as it’s also commonly referred to, two metal specimens are joined together through an electrode. The electrode refers to the tool or material that’s used in order to allow the passage of electrical current from the welding machine, onto the workpiece. This is also the tool that’s responsible for creating the arc that effectively joins the two materials together.
In this welding type, non-consumable tungsten is used. This means that as the welding process takes place, the electrode material doesn’t melt due to the high melting point of tungsten — 3,422°C, to be exact.
The GTAW technique is considered to be one of the most difficult welding techniques to learn, primarily because the welder has to see to it that the length of the arc is short while ensuring the electrode doesn’t touch the workpiece.
Despite this, it’s considerably cleaner compared to other techniques, since it doesn’t produce any debris or metal slag. This is the ideal welding process for thin-walled alloys and metals like aluminum, stainless steel, or copper.
Gas Metal Arc Welding
Unlike in GTAW, Gas Metal Arc Welding (GMAW) or Metal Inert Gas Welding (MIG), the welder uses a consumable piece of an electrode in order to incorporate the two materials together. This method is also far simpler to perform and can be learned without extensive professional training.
In this technique, the electrode wire does not have a coating and it is heated up until the melting point. Because most of the gas expelled during the process is produced by the molten tip of the electrode, the entire welding operation needs to be protected using either one of the following: carbon dioxide, argon, or helium.
While the first technique might be more applicable to alloys, GMAW on the other hand is best suited for low-alloy-containing steel, carbon steel, nickel, aluminum, titanium, or copper.
Flux Cored Arc Welding
Flux Cored Arc Welding (FCAW) can be conducted with or without the presence of shielding gas. This is because of an important component called the flux. Basically, this material is responsible for preventing the welded workpiece to be subject to external contamination.
When the welded material is contaminated, this could negatively affect the quality of the process. This is due to the oxidation that occurs on the surface of the workpiece. As the byproduct of chemical reactions between the weld and the surrounding, the flux in FCAW is used to protect the specimen.
The weld flux also helps the weld maintain a slow cooling rate in order to prevent early or unwanted solidification. This is especially evident in cases wherein the continuously-fed electrode is used on low-alloy, high-strength steel, stainless steel, as well as steel that has a high abrasion-resistance rating.
Electron Beam Welding
One advantage that the Electron Beam Welding (EBW) technique has over all the other welding processes on this list so far, is that the material is far less prone to contamination due to oxidation. This is because the process is done in a highly-controlled environment where atmospheric contamination is less likely.
Due to this high-precision welding technique, it’s usually done with the use of a computer-controlled or an automated machine. In this process, the electron stream/beam that is produced through thermionic emission (electron discharge) is focused on the workpiece. Due to the high-intensity process, it effectively liquefies the metal and requires less heat compared to the typical arc welding.
EBW is mostly used for welding aerospace, medical equipment, automotive components, as well as industry-specific parts that require high-accuracy and precision in dimension.
Atomic Hydrogen Welding
Atomic Hydrogen Welding (AHW) involves the use of two non-consumable tungsten electrodes. While the use of tungsten may be similar to the GTAW process, the welder has more freedom in adjusting the distance of the electrodes from the workpiece in order to modify the amount of heat that is generated in the arc.
Due to the large head production that results from the AHW technique, it’s considered to be one of the highest-temperate welding techniques to work with. It may even be capable of melting tungsten — which, as mentioned before, has an incredibly high melting point of almost 3,500°C.
One unique feature about AHW is that the hydrogen produced in the atomic reaction acts as the shielding gas to protect the workpiece. There is no longer any need for any external gas or a weld flux in this regard.
Key Takeaway
The different types of welding processes include Gas Tungsten Arc Welding, Flux Cored Arc Welding, Electron Beam Welding, Atomic Hydrogen Welding, and Gas Metal Arc Welding.
There is no single welding technique that is considered to be the most effective since different types of alloys or metals have different requirements. Likewise, they also have differing applications. For example, industries that may require high-precision welded parts might benefit better from EBW, while a simple arc welding technique may suffice for low-precision activities.
Nevertheless, all of these welding techniques need to be done correctly to prevent defects that can corrode the material or reduce the quality of its condition. Make sure that you’re choosing the most appropriate technique before fusing two metal or alloy materials together.