What Are the Different Types of Heat Treatment Methods?
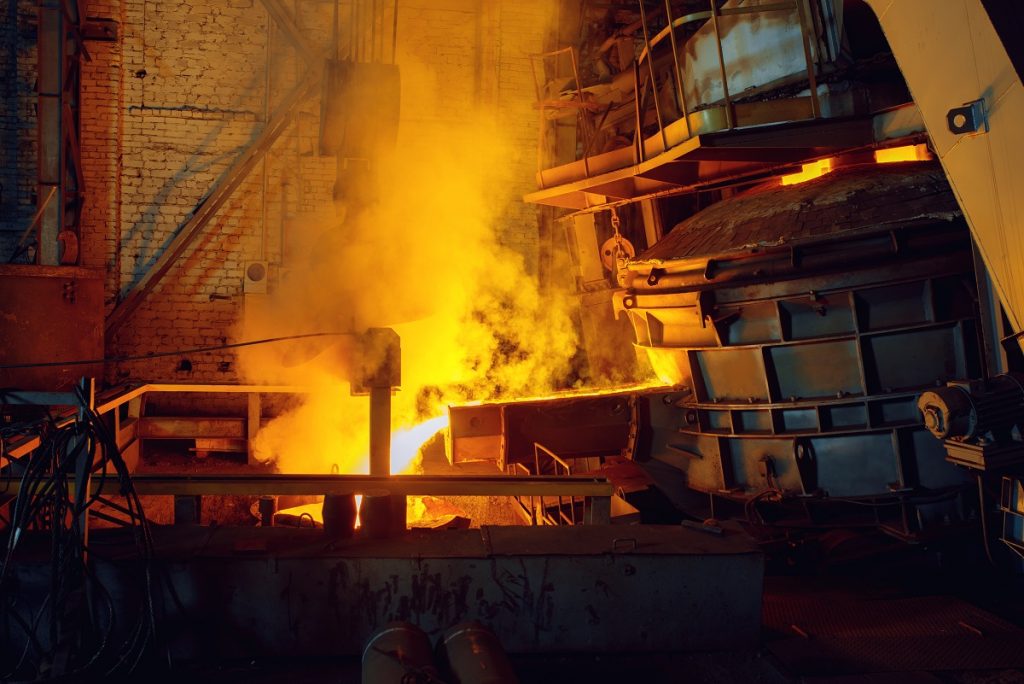
What are the different types of heat treatment methods?
- Hardening
- Annealing
- Normalizing
- Carburizing
The different types of heat treatment methods are typically applied to alloys such as steel. The purpose of these treatment processes is to create alterations within the material’s grain micro structuring. Manufacturers usually want to enhance or achieve the desired property of the metal, which is why they subject the material to heat treating. For example, they may want to improve the material’s surface hardness, core hardness, ductility, machinability, strength, tensile strength, and many more.
In this list, you’ll find the following methods: hardening, normalizing, annealing, and carburizing. Continue reading to learn more.
Hardening
Most of the heat treatment methods that you will encounter involve stages wherein the alloy specimen is left to cool at room temperature, or are directly subject to a cooling method. The rate at which cooling is done is dependent on which of the properties of the alloy that the manufacturer wants to highlight.
Hardening is one of the most common forms of heat treatment that’s designed to create improvements in the physical and mechanical properties of the material. First, the alloy material is subjected to temperature above its critical transformation temperature. When we’re talking about the hardening of steel, for example, this temperature falls beyond 724 degrees Celsius. At this point, the steel’s crystallization is manipulated, and then it starts to recrystallize as austenite.
After, the metal will be cooled through different mediums — air, oil, water, or other substances. Through the hardening process, the material’s strength and hardiness are increased. This allows it to better withstand impacts and pressures that may have otherwise caused the metal to deform without hardening.
Annealing
Unlike the hardening process, the annealing process aims to alter the mechanical and electrical properties of the alloy. Even more so, annealing is done in order to reduce any stress in the grain micro structuring of the alloy and subsequently improve its ductility — the point at which the metal can be stretched or deformed without fracturing.
Many types of alloys and metals can be subject to annealing, such as copper, brass, aluminum, or silver. With this in mind, the annealing temperature may vary across metals and alloys. Steel annealing, in particular, requires that the metal be heated around 38 degrees Celsius above its critical temperature of 724 degrees Celsius. It typically involves three other stages, namely recovery, recrystallization, and grain growth.
- Recovery – The material first has to undergo a low-temperature heat treatment which is necessary to restore the physical structure of the material.
- Crystallization – After the application of further heat, recrystallization of the material takes place. This is done to further eliminate the impurities in the grain structuring
- Grain growth – Finally, the material is subject to further heat in order to make its grain structure more consistent. As the name suggests, the grain begins increasing in size, which makes them coarser. This reduces the material’s hardness and increases the overall ductility.
Normalizing
The normalizing heat treatment process is similar to annealing, however, with a few key differences. In normalizing, the material has a faster rate of cooling. While this results in a more ductile material, the faster cooling rate creates a ductile, yet hard material that’s significantly more durable compared to another material that has been annealed.
Typical metals that can undergo normalizing include the following: copper, brass, aluminum, carbon steel, stainless steel, and other nickel alloys. This method is significantly more cost-effective and economical compared to annealing because the material spends a shorter duration being cooled in a furnace.
These metals and alloys can greatly benefit from normalizing because it not only improves its ductility, but it also makes the metal more machinable. This allows manufacturers to more easily alter the physical properties of the material and fabricate it to produce beams, sheets, pipes, corrugated sheets, trusses, and the like.
Carburizing
Carburizing is done on low-carbon steel, or steel alloys that have a carbon content of less than 0.3%. This means that there is a higher presence of iron in the material, which makes the steel more vulnerable to different forms of corrosion like cracking, oxidation, pitting, and the like.In carburizing or carburization, the low-carbon steel is subject to high temperatures inside a vat or a furnace, wherein it begins transforming into a high-carbon material. This process can be further categorized into vacuum, liquid, gas, or pack carburization, but we can touch up on only the first two to better illustrate the process.
Vacuum Carburization
In this vacuum method, the low-carbon alloy or steel is stored inside a vacuum furnace where it is heated at temperature ranges of 350 to 550 degrees Celsius. After, the metal is exposed to propane gas which is broken down into hydrogen, hydrocarbon, and carbon. The carbon elements then diffuse towards the low-carbon steel to harden it.
Liquid Carburization
Liquid carburization is done in a molten salt material — usually a cyanide-containing compound. Upon submersion, the metal specimen gets into contact with the carbon molecules in the liquid bath, allowing them to diffuse and then increase the hardenability of the metal in the process.
Key Takeaway
As you’ve learned, many types of heat treatment methods are done in order to highlight a particular property of the alloy or metal. Some techniques — like carburization — are typically applied to materials that have a high iron and low carbon content in order to harden it. For other processes such as annealing and normalizing, on the other hand, the quality of the metal’s hardness and ductility is influenced by the rate of cooling.
With these heat treatment techniques, manufacturers have been able to maximize the fabrication of different metal products. The resulting material can then be used for structural or other industrial processes.