6 Benefits of a Press Brake in Metal Fabrication
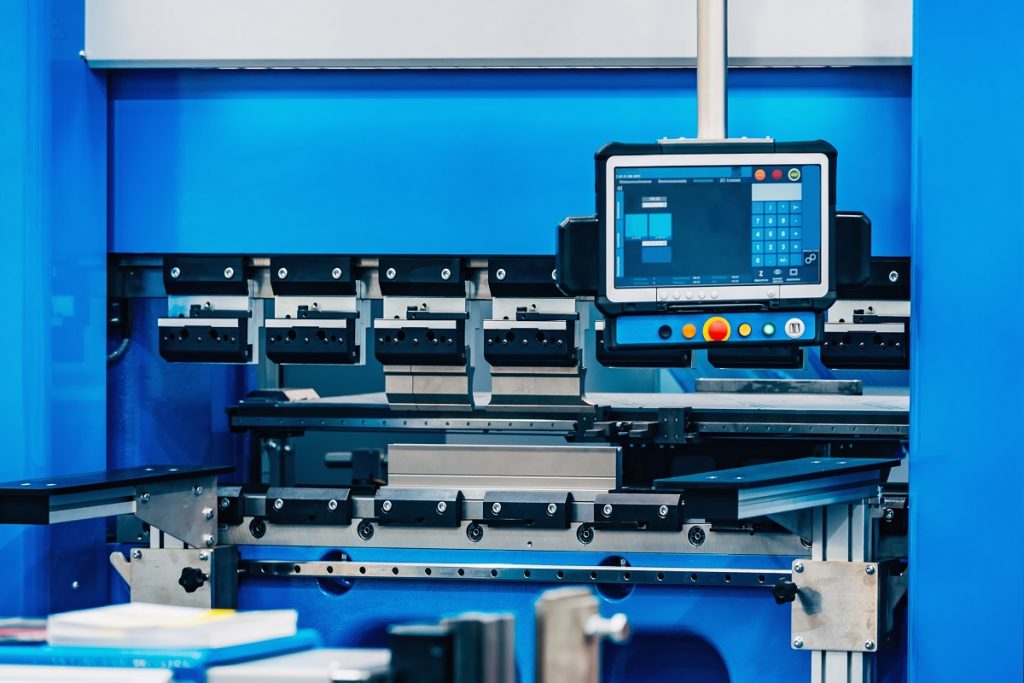
What are the benefits of a press brake in metal fabrication?
- Less material waste
- Increased productivity
- In-house manufacturing capabilities
- Versatile programming
- Automation
- Complex designs
A metal fabrication company that aims to consistently meet customer demand can do so with press brake machinery. The many benefits of press brake metal fabrication have offered manufacturing firms better tolerances, capacity for complex operations, automation, and an overall improvement in efficiency.
The press brake is a type of equipment capable of performing a number of functions, such as punching, bending, cutting, stamping, blanking, and many more. Several industries have taken advantage of this machine to come up with customized, aftermarket, and OEM-designed parts from simple sheet metal.
From its origins as a simple mechanical press brake in the early 20th century, modern reiterations continue to uphold the press brake’s early legacy as some of the most useful machines for manufacturing. Read on to learn more.
Less Material Waste
Compared to other fabrication methods, the press brake is known to produce less material waste. The main driver behind this is that it is capable of curving, cutting, or bending sheet metal into accurate pieces. Since it is often computer numerically controlled (CNC), press brake processes are typically automated. All of its components — the dies, punches, rolling carts — can all follow a well-set-up procedure that simply works.
With this in mind, the minimal waste produced allows operators and firms to complete press brake operations at the fastest time possible. This greatly shortens the manufacturing lead time, lowers the cost burden on the customers, and minimizes the need for secondary/post-processing on the fabricated metal part.
Increased Productivity
Defects are part and parcel of every type of manufacturing. The goal has not been to eliminate them, but to reduce their occurrences, such that they do not affect the normal flow of operations and productivity. After all, defects can significantly impact the production process through increased downtimes and slower deployment for assembly or distribution.
Machinery like the press brake is wholly capable of this, which is why they’ve been used for improving productivity outcomes. As long as any fabricator or equipment operator has undergone proper training, they can operate various types of press brake machines with ease.
More advanced models of the press brake, in particular, can perform several hundreds of bends all at once, facilitating high-volume production. Easy to set up and minimally-intensive, the press brake is a productivity solution that many industries can benefit from.
In-House Manufacturing Capabilities
Owning a press brake machine allows companies to partially or completely divert their manufacturing in-house. Especially where sheet metal bending or fabrication is concerned, in-house production eliminates the need for offshoring which can not only be expensive but also unable to sustain demand.
Instead of hiring third-party companies for metal fabrication, companies can simply invest in advanced press brake machines. This is cost-effective in the long run due to the low investment needed for training, as well as, a renewed focus on in-house development.
Versatile Programming
Simple production techniques continue to be useful, but they’re best complemented by press brakes, which are capable of versatile programming. Operators can define the machine’s parameters in order to perform the intended coning, material thickness, flange dimensions, angle bends, inside radius, blank size, and many more.
With the number of functions that can be done on a press brake, it’s flexible enough to be used with different types of raw materials and sheet metals. Further, companies can consistently come up with a wide variety of tooling designs and prototypes as needed.
Automation
Press brakes can be manually operated, semi-automated, or fully automated, depending on the requirements. Nevertheless, all of these machines are critical in improving the accuracy of parts and reducing overall labor costs.
Automation allows for faster completion of tasks that were previously done manually. Press brakes are instrumental to this, as they can speed up fabrication, shorten lead times, and even improve overall workplace safety. Companies looking to meet client demand can rely on this type of equipment to boost production rates, productivity, and daily processes.
Complex Designs
Sheet metal fabrication has been a fixture for almost all industries. Construction companies, for example, rely on fabrication to build beams, rafters, and other structural materials to bring high-rise developments to life. For the food & beverage industry, on the other hand, metal fabricated parts are needed in creating foodservice equipment like mixers, conveyor belts, metal weighing scales, and many more.
From the beginnings of a press brake as a simple tool for bending sheet metals into shape, it has since paved the way for modern machinery capable of complex designs. Most press brakes to date come with customizable parts and components, enabling various manipulations, like bends, coining, burring, and many more.
Key Takeaway
At first glance, the press brake seems to be simple manufacturing equipment that bends sheet metal into different shapes. However, its impact on the manufacturing sector cannot be underestimated.
The benefits of the press brake in metal fabrication have led to better outcomes by speeding up manufacturing, enabling complex designs, reducing waste, and enabling in-house production. Industries will continue relying on this machine to satisfy fabrication requirements intended for assembly or final distribution.