6 Factors That Can Corrode Stainless Steel
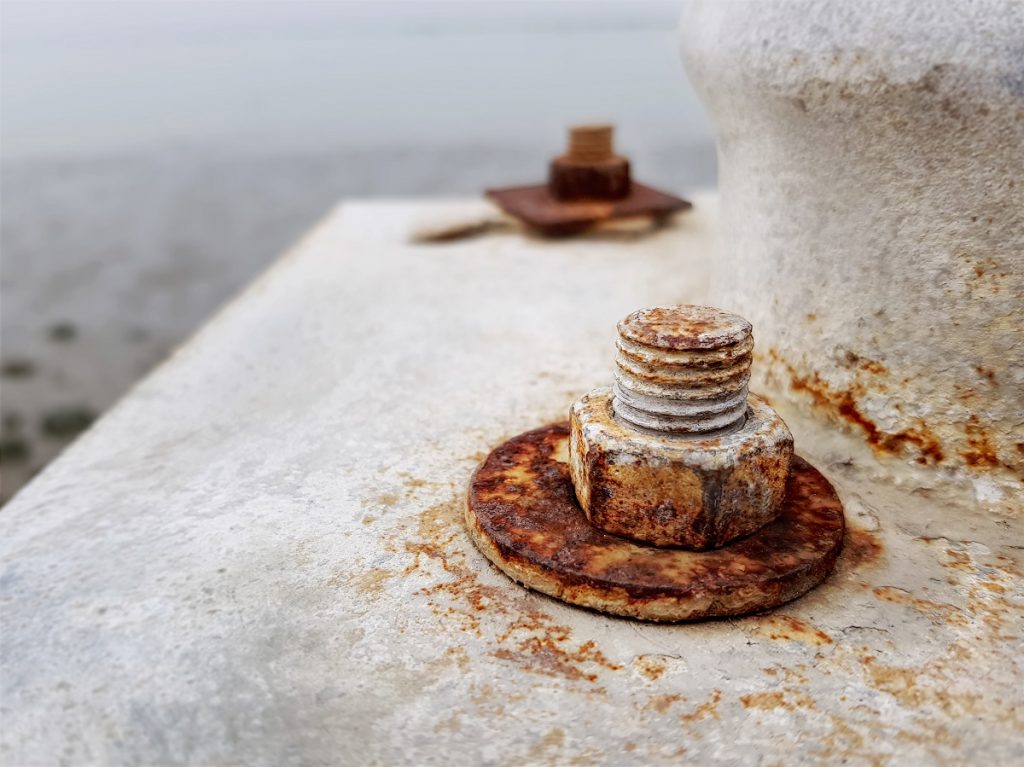
What corrodes stainless steel?
- Acid Immersion
- Strong Chlorides
- Galvanic Reactions
- Transplanted Plain Iron or Steel
- Lack of Oxygen
- Temperature Extremes
Stainless steel is an alloy made from iron, chromium, and other metals. This material is well-known for its resistance to environmental factors like corrosion. However, its increased resistance doesn’t mean that it is completely impervious — under certain circumstances, this material can corrode, and cause many problems for its users. This post dives into what corrodes stainless steel, and what factors and practices you should avoid when using this metal product.
How Stainless Steel Can Resist Corrosion
There are multiple stainless steel alloys and grades that differ in their metal composition, alloying process, and manufacturing methods. The one trait that all stainless steel alloys share is their passivation layer. This layer is made of chromium oxide and is formed when the surface of the metal is exposed to oxygen.
The passivation layer is impervious to water, is self-generating, and helps to protect the stainless steel from rust and corrosion. It can also withstand high heat without melting — though it can get discolored over time.
This passivation layer is not invincible, and corrosion may still occur under the right environmental circumstances. Furthermore, as there are various alloys of stainless steel, the factors that may cause one alloy to corrode may not affect another one.
Acid Immersion
Generally, stainless steel alloys are resistant to acid. However, the levels of resistance will depend on the alloy being used, the concentration and type of acid, and environmental temperature.
When stainless steel is immersed in acid, the passivation layer may be affected. When this occurs, the layer is eaten away uniformly, and corrosion will occur over the entire surface of the metal. Sulphuric and hydrochloric acids can be particularly aggressive against most stainless steel alloys, especially when in high concentration.
One way to avoid this is to choose a grade of stainless steel that is appropriate to the acidic environment you want to use it in. For example, when working with hydrochloric acids using 304 stainless steel is not recommended. Instead, using a 400 series stainless steel would be more acid-resistant.
Strong Chlorides
Pitting corrosion can occur when stainless steel is exposed to chloride-rich environments. For example, stainless steel plates used in cargo ships experience pitting over time, which is a result of being in constant contact with seawater and sea breezes — both of which contain high levels of salt.
To avoid corrosion due to strong chlorides, you can choose a grade of stainless steel that is specifically designed to resist the chemical — such as 316 stainless steel. Avoid using grades that are known for their weak resistance to chlorides — like 304 stainless steel. Aside from that, specialized coating to decrease direct contact with chlorides can also be used.
Galvanic Reactions
When two metals with different galvanic potentials are welded or in contact with one another, it can cause corrosion. This happens when the connection via electrolytic material leads to an unbalanced flow of electrical current from one metal to another. One metal will accept more electrons, turning it into an anode, which then causes corrosion.
While problems with galvanic reactions seldom happen between two stainless steel of different grades, they can still occur depending on the grades used. This reaction can also happen when using this material with another metal, such as graphite.
The rate of corrosion is affected by the type of stainless steel used, welding filler used, temperature and humidity, and the surface area of the metals in contact with the other.
The best way to prevent this is to avoid using two dissimilar metals in one project. Another way is to add a protective coating to the metals in order to prevent the flow of electrons from one metal to another. You can also break this connection using insulation, which separates the two metals from each other.
Transplanted Plain Iron or Steel
Plain iron and steel residue may accidentally be transferred onto a stainless steel part in the manufacturing process. These particles can affect the quality of the stainless steel, and disrupt its natural resistances to environmental factors — including corrosion.
One way that this can happen is when equipment is used to process multiple kinds of materials and is not properly cleaned or inspected in between batches. Residue from a previously processed batch can stick on the tool’s surface, and transfer onto stainless steel.
To prevent this from happening, it is important that manufacturers thoroughly clean equipment after each batch is done processing. Additionally, it is advisable to never use certain equipment for different metal types — such as steel brushes. This is because it is difficult to fully remove all particles of one material from the surface.
Lack of Oxygen
The passivation layer needs a constant supply of oxygen to sustain itself. In tight and small crevices, it is not possible for enough oxygen to reach inside. This oxygen deprivation can cause the stainless steel to be vulnerable to attack.
These tight crevices can also allow chlorides and acids to concentrate on the metal surface while preventing oxygen from entering. This speeds up the corrosion process.
This can be prevented by sealing crevices in your stainless steel material with flexible sealant. Using proper welding techniques and ensuring drainage can also prevent the creation of additional crevices.
Temperature Extremes
Stainless steel is designed to have a high melting point (usually above 600˚C). While it can withstand temperature extremes without melting, this can still affect it in ways that impair its ability to resist corrosion.
One common example is when stainless steel alloys are exposed to high temperatures and form scales. These scales are made from leftover metal particles that are fused together during the heating process. This can cause galvanic corrosion, as the scales have a different composition from the base stainless steel material.
Temperature extremes can also cause stainless steel to lose its passivation layer for a period of time. This layer will take some time to reform after being stripped away by the heat. Without this layer, the risk of corrosion increases.
To prevent this from happening, check the recommended operating temperatures for the grade of stainless steel being used. If the temperatures in your project or operations exceed those limits, consider adjusting temperatures or procuring a grade of stainless steel that better matches your needs.
Key Takeaway
Preserving the quality of your stainless steel products is all about knowing what can affect the material’s integrity and natural resistance properties. Knowing what corrodes stainless steel will help you keep your products structurally sound and usable for as long as possible.
For those wanting only the best quality metals, knowing additional prevention measures as well as receiving professional insights is recommended. Contact Metal Exponents today to consult experts on ideal fit and safety precautions for your stainless steel products!