4 Defects in Galvanized Coatings
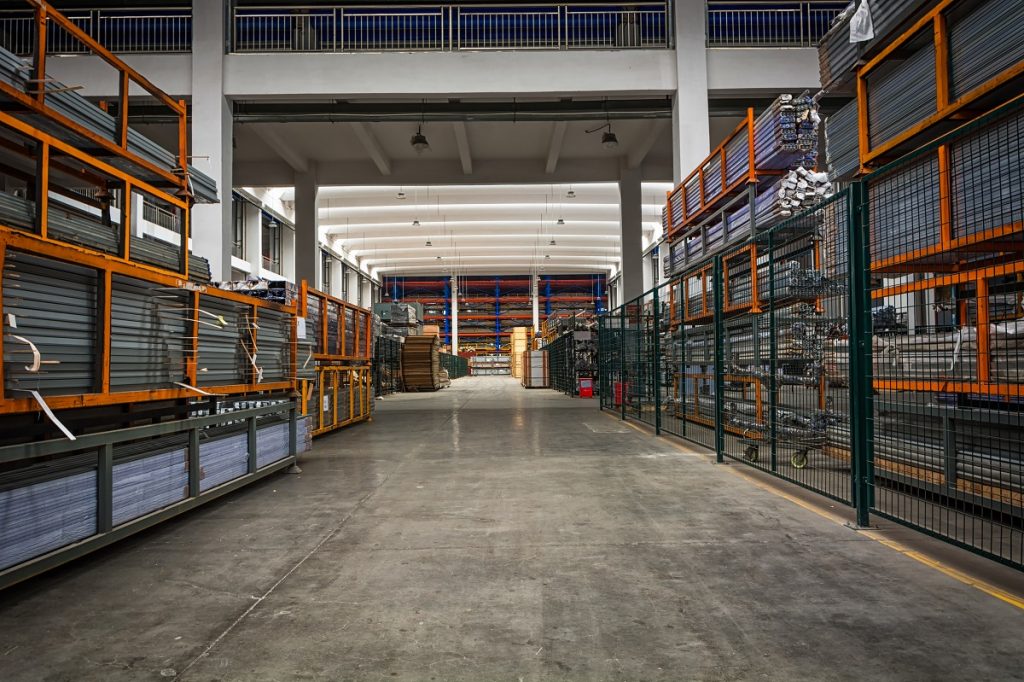
What are some defects in galvanized coatings?
- Ungalvanized parts
- Dark stains
- Embrittlement
- Uneven surfaces
Many of the defects in galvanized coatings can be attributed to the method of galvanization, speed, temperature, or even the appearance of the material. As much as the metal fabricator tries to avoid problems in the galvanization process, they may not necessarily be completely unavoidable.
The galvanizing method, after all, requires precision. Different types of techniques like hot-dip zinc galvanizing, electroplating, thermal spraying, and the like, are employed to make sure that the process is done right. Even if just one aspect of the technique is compromised, it could be the result of issues and surface deformations such as ungalvanized areas, embrittlement, stains, or uneven surfaces.
Avoiding any issues on the galvanized material should be done as part of stringent Quality Control and to make sure that the finished product is well-suited for its intended use — be it structural or not. Read on to learn more.
Ungalvanized Parts
Like with many coating processes, surface treatment or surface preparation should be done before anything else. The surface of the metal specimen should first be inspected and assessed in order to remove any debris, dirt, grime, or any other unwanted substances.
In the case of ungalvanized parts, this is oftentimes caused by the presence of weld slags on the material. These are common in the arc welding process, wherein a molten flux invariably attaches to the welded material. Although welders see to it that this slag is eventually scraped away from the product, there are some cases where it may be overlooked.
As such, during a process like hot-dip galvanization, the molten zinc won’t be able to adhere to the metal because of the weld slag. But removing this piece of unnecessary material can be done easily through simple tools like a chisel or a small hammer. The slags should come right off easily because of their loose attachment to the metal.
Dark Stains
Dark stains are usually spotted right after the galvanizing process has already been completed. These are also sometimes referred to as “wet storage stain” to refer to the markings that may form on the metal while it’s being stored through stacks or rows under non-ideal conditions.
In storing galvanized finished products, the conduciveness of the location should be a key priority. The materials shouldn’t just be stacked haphazardly, especially in an environment that has high levels of humidity. As much as possible, the facility should have proper ventilation and is free from any potential sources of moisture.
In the event, however, that these stains may still occur on the metal, removing them is the next best choice. This can be done by using a metal wire brush that’s been dipped in a vinegar solution.
To make sure that the quality and thickness of the zinc coating aren’t affected after brushing the material, it’s also advised to conduct measurements before and after the brushing is done.
Embrittlement
Sticking with the hot-dip galvanizing method, another defect that can occur is called embrittlement. This is less common in steel products that mainly have a structural application, but can take place in steels that have a high-strength grade. Some examples would be Dual-Phase (DP) steel, Hot-Formed (HF) Steel, or Martensitic (MART) Steel.
Embrittlement appears like small cracks on the coated material’s surface. This is caused when hydrogen molecules escape from the steel grain structuring during galvanization. Due to significant internal stress and pressure caused by high yield strength and the temperature of the molten zinc bath, the hydrogen will get stored inside the structure and will be released after some time. The result is a cracked material that has lower durability.
To avoid embrittlement, the steel material that’s coated should have a yield strength rating lower than 170ksi. If this isn’t possible, then the focus should be put towards ensuring that the surface preparation process is done meticulously, or by dipping the steel in acid (acid pickling) to minimize the hydrogen presence inside the grain structure.
Uneven Surfaces
The entire steel or iron specimen can also be distorted during galvanization. For sheet metals, this can cause the product to have irregular surfaces. One area of the metal may be bent, which lowers its functionality once used as wall paneling, flooring, roofing, and the like.
These uneven surfaces can be typically found in steel parts that don’t really have a high level of structural integrity or dimensional stability. Take for example angled steel bars or steel channels. Compared to a W-Beam or I-Beam, steel bars and channels are far more prone to this type of defect during the galvanizing process.
As with many of these defects, preventive measures should be taken to avoid them. The design of the product should conform to the standards that were previously noted. More than that, the experience and skill of the galvanizer should also be taken into consideration to make sure that the speed, temperature, and pressure are at the correct rates while maintaining the accuracy of the process.
Key Takeaway
Some of the defects in galvanized coatings are the following: ungalvanized parts, uneven surfaces, distortion, or embrittlement. Most of these issues can be avoided by simply ensuring that all the phases and stages in galvanization are adequately controlled.
Certain adjustments can be made to the quality of surface preparation, type of metal specimen, speed of galvanization, temperature of the molten zinc, or the rate of cooling.
Despite most of these issues only having aesthetic implications, they may eventually have functional effects that should be avoided at all costs, to retain the zinc coating’s efficiency and durability.