What are the Different Methods of Galvanization?
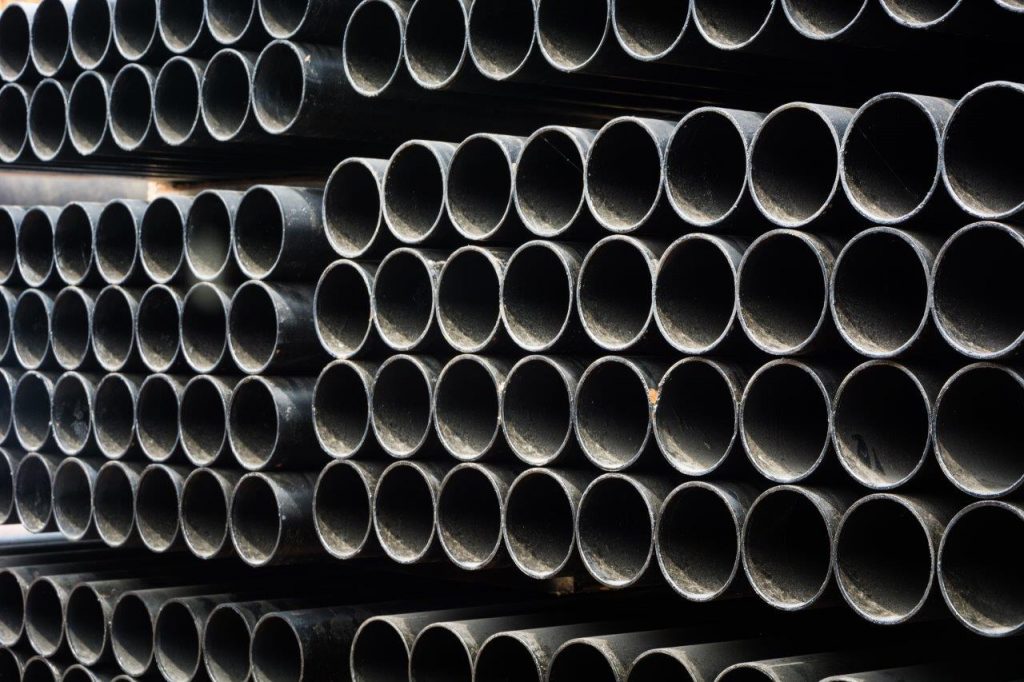
What are the different methods of galvanization?
- Thermal spray
- Electroplating
- Sheet galvanizing
- Hot-dip galvanizing
Steel is undoubtedly one of the most common materials used in many different industries. Its many attractive qualities like durability and malleability allow it to be utilized in construction projects, industrial operations, as well as many other residential and utility-related undertakings. When it comes to steel product production, manufacturers employ different methods of galvanization in order to enhance the other qualities of steel.
Typically, not all manufactured steel presents some form of resistance to corrosion and other forms of oxidation. Similar to iron, steel is a non-ferrous metal which can be further exposed and subjected to different elements in the environment. Through a method known as galvanization — which simply refers to the application of a protective coating of zinc on the two metals mentioned above — steel or iron items would be able to better withstand corrosion.
There exist many methods of galvanization which differ from one another in terms of the material used, the thickness, as well as the type of processes that are included. Continue reading to learn more about these different methods.
Thermal spray
Galvanizing is a method which is employed in manufacturing steel and iron items in order to increase the level of corrosion resistance they possess. In the process of thermal spray, a material such as zinc wire undergoes a semi-molten process. As noted by the name of the process itself, the molten zinc wire is then projected through compressed air into a workpiece.
Thermal spray produces the thickest coating of zinc out of all the other methods of galvanization which would be encountered in this article. Before engaging in any kind of galvanizing process, it’s important that the material is coated with zinc and undergo sufficient surface preparation in order for the coating to adhere more effectively to it as well as prevent the formation of any kind of irregularity.
Grit blasting is typically the most effective method of surface preparation before subjecting a particular steel material to the thermal spray process. Simply put, this involves abrasive particles which are fired through a nozzle through the use of compressed air in order to remove sand on the surface of the material.
Electroplating
Unlike the thermal spray method, electroplating generally yields the least thickness when it comes to applying a layer of zinc coating to steel products. This method is typically utilized on smaller items such as fasteners and other useful everyday materials.
Electroplating refers to the process of passing a constant electric current through a solution referred to in this method, as an electrolyte. This is a more complex form of galvanizing and was employed in the past in coating other metals and materials with cadmium, instead of zinc. In the electroplating process, materials such as a rectifier, plating station, ancillary tank, zinc anode, and a reservoir are used.
Similar to the thermal spray method, however, one should prepare the surface of the material for the galvanizing process. An effective solution to clean surfaces is that of an alkaline detergent, which is followed by the application of an acid treatment to further remove rust and debris on the surface. After which, the material to be coated is submerged into an electrolyte zinc solution, where galvanization takes place.
Sheet galvanizing
The sheet galvanizing method is typically employed with steel sheets and other kinds of steel materials such as wires in order to increase their resistance to oxidation. The resulting layer of coating is thicker compared to materials which undergo electroplating, but thinner compared to the thermal spray method.
Also known as continuous sheet galvanizing, this method is a coil-to-coil process wherein a steel sheet, wire, or strip undergoes a constant pressure through a continually-moving ribbon which applies a layer of zinc that bonds with the material. The resulting thickness can range from around 1.70 inches to as much as 72 inches, depending on the desired figure.
After surface preparation of the steel, the material undergoes a method of annealing in order to increase its strength, and formable properties. This is also a way to remove other unwanted substances from the material before it undergoes galvanization.
Steel sheets that have undergone this galvanizing method have a wide variety of applications, including in-car bodies, corrugated roofing materials, piping, and the like.
Hot-dip galvanizing
Hot-dip galvanizing is another common type of galvanizing method which involves the immersion of a material into a pool of molten zinc which adheres to the former’s surface.
In this process, the temperature of the molten zinc is maintained at around 460 degrees Celsius. The zinc coating bonds with the material in a metallurgical reaction which takes place between the steel material, for example, and the zinc. After dipping the material into the bath, it is pulled out from the solution. A reaction then transpires between zinc and oxide particles in the air, making the final zinc-oxide protective layer.
Key Takeaway
While the inherent qualities of steel are already attractive enough for different industries to utilize this kind of material in various processes, manufacturing processes make use of the different galvanizing methods in order to improve steel’s resistance to corrosion.
In essence, zinc is the most common material which is utilized in order to add a protective layer to non-ferrous metals like steel and iron. Ultimately, there is no single way in which galvanization is utilized in many processes. With the guide above, you’ve been hopefully equipped with adequate information on the different kinds of galvanization methods, their processes, and their applications to many steel industrial manufacturing.