How To Choose The Right Sheet Metal
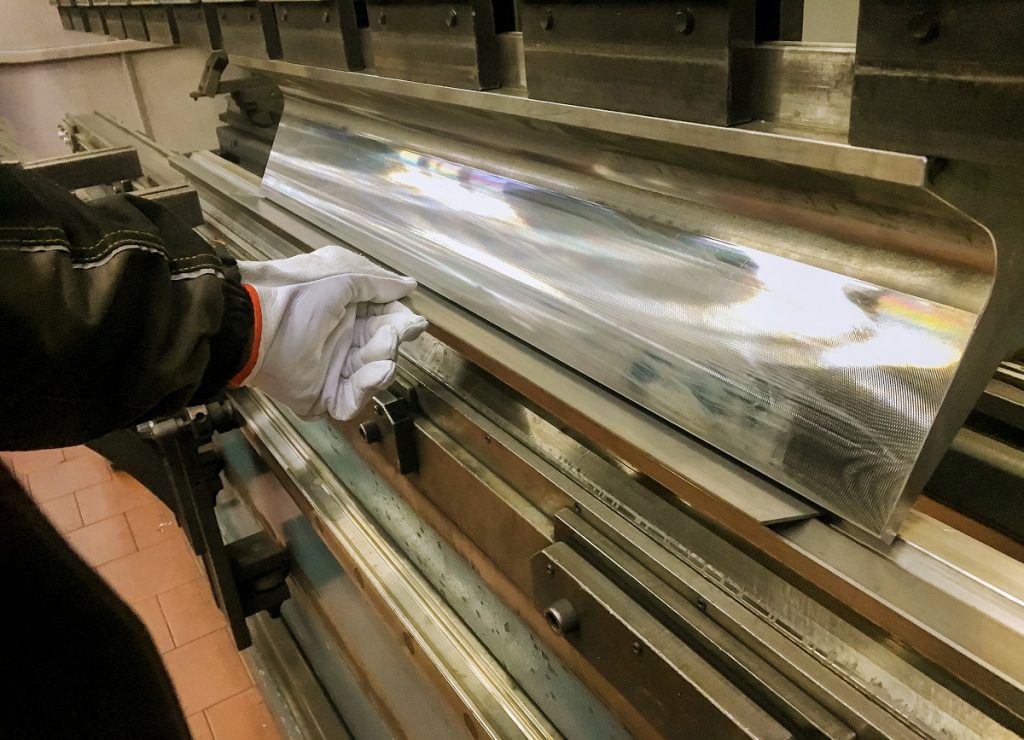
How can you choose the right sheet metal?
- Consider desired material and size
- Explore sheet metal alloy options
- Check design and tolerance
- Factor in manufacturing processes utilized
- Factor in fabrication processes utilized
- Factor in finishing options
Let’s say you have a metal project to create, but you’re not sure what sheet metal to choose. Choosing the right one is crucial to ensuring your manufacturing process goes smoothly, and the resulting parts can perform as designed. To choose the correct sheet metal for the job, there are several factors to consider and several requirements to meet. Here is our simple guide on how to choose the right sheet metal to help you get started on your material selection process.
Consider desired material and size
First, consider how the material needs to perform for your application, and what form your design is aiming for. Ask these questions to help you narrow down your desired material and size:
- How big, small, wide, or narrow should the sheet metal be?
- How strong should the sheet metal need to be?
- What requirements should the sheet metal meet in terms of weldability, ductility, machinability, and tensile strength?
- Is there a specific strength-to-weight ratio the sheet metal needs to meet?
Lastly, consider your overall budget for your project. Sheet metals that can perform extremely well in most (if not all) aspects tend to be more costly in the long run. Additionally, some sheet metals that meet your requirements may not be widely available — which also increases cost. Weigh your requirements against your budget and consider what areas you need to adjust in and which ones are non-negotiable.
Explore sheet metal alloy options
There are many different kinds of metals and metal alloys used to make sheet metal and are used in the fabrication of metal products. Depending on what metals they’re made from, they have varying strengths and weaknesses regarding their formability, weldability, corrosion resistance, strength, weight, and cost.
Most common materials found in sheet metal fabrication include:
- Aluminum — One of the lightest options, possesses excellent corrosion resistance, is thermally and electrically conductive, and offers a variety of grades for customization.
- Stainless Steel — Comes in a wide range of grades, and possesses excellent corrosion resistance, impact resistance, strength, and sterility. Some grades are non-magnetic while others are magnetic.
- Pre-plated Steel — Also known as galvanized steel. Coated in a protective zinc layer which enhances rust and corrosion resistance. Typically more ductile and easier to fabricate.
- Cold-Rolled Steel — Has a smooth surface finish and is capable of meeting complex geometries and following tight tolerances.
Check design and tolerance
While material requirements play a big role in sheet metal selection, your chosen design and tolerances matter as well.
The shape and complexity of your design will dictate which sheet metal option is the best pick. Different grades, alloys, sizes, and thicknesses will dictate whether the sheet metal is suitable for simple designs, or is capable of fulfilling complex geometries.
The size and complexity of your component combined with the material choice will dictate whether or not the sheet metal is suited for your needs. Factors to consider include:
- The complexity of your component’s geometries
- Performance considerations like weldability or tensile strength
- Wall thicknesses
- Bend allowance
- K-factor
- Orientation of holes and slots
Factor in manufacturing processes utilized
The sheet metal should not only fulfill the design you have in mind, but also the manufacturing processes needed to make that design a reality. Your best choice should be capable of withstanding all the manufacturing it may need to undergo until it becomes a complete, finished product.
Some common manufacturing processes to consider during your sheet metal selection process are:
- Laser cutting — Used for precision designs with tolerances up to +/-0.005″
- Waterjet cutting — Utilizes a high-pressure water jet containing abrasive particles to cut sheet metal. Typically used for thicker, sturdier metals (up to 150mm thick).
- Bending dies — Applies stress to the sheet metal to create bends. Examples include U-bend dies, V-bend dies, goose-neck dies, and the like. Appropriate dies depend on the sheet metal bending design considerations.
- Mechanical punching — Used to create a hollow or curved surface on sheet metal. Performed by drawing the piece into a die.
- Annealing — Softens and improves the machinability of sheet metal and may enhance electrical conductivity.
Factor in fabrication processes utilized
Fabrication, which involves finishing up the initial manufacturing process through enhancing or maintaining the shape and integrity of the product, is also something to factor in.
Techniques used in fabrication, such as welding and riveting, affect sheet metal in many ways. The appropriate processes to use to finish the product will largely depend on the sheet metal and how it may react to the fabrication process.
Common fabrication techniques to consider are:
- TIG Welding — Uses tungsten inert gas rather than filler metal. Creates a strong, high-quality, precise weld.
- MIG Welding — A cost-effective, clean, and quick option compared to TIG welding. However, it tends to be less reliable and may be hazardous when used on certain metals.
- Metal Stamping — Cold-forming process that uses dies and stamping presses against sheet metal. This is done to reform it into different shapes.
- Cutting — Performed with various mechanical and automatic cutting tools to remove unwanted parts.
Knowing the different fabrication processes and what they entail is important. This understanding will help you choose the appropriate sheet metal and know-how that will directly affect the final stages of manufacturing.
Factor in finishing options
Last is the finishing options. Depending on what kind of sheet metal you’re using, some finishing options will protect the metal from elements like corrosion, while others are done purely for aesthetics. In some cases, finishing can achieve both purposes.
Typical finishing techniques include:
- Brushing — Used to remove surface defects from sheet metal. Creates a uniform parallel grain as the brush moves against the sheet metal’s surface.
- Plating — Coats another layer of metal onto the sheet metal. This is commonly used for aesthetic purposes.
- Polishing — Uses coarse grit sandpaper to smooth out the sheet metal, remove imperfections, and create a gleaming surface.
- Powder Coating — This makes a hard finish that is more durable than conventional paint. Provides both practical and aesthetic benefits.
- Sandblasting — Applies a stream of high-pressure abrasive material to the sheet metal. Done usually to roughen a smooth surface, shape the sheet metal, or remove surface contaminants.
Key Takeaway
Not all sheet metals are created equal. The right sheet metal for your project will depend on many factors, such as the ones mentioned in our guide on how to choose the right sheet metal.
To help you choose the right materials and manufacturing processes for your metal parts and components, you also have to select the right partner — Metal Exponents. We can help you close the gap between your ideal design, the best sheet metal, and the optimal manufacturing processes. Contact us today to start!