6 Methods of Metal Casting
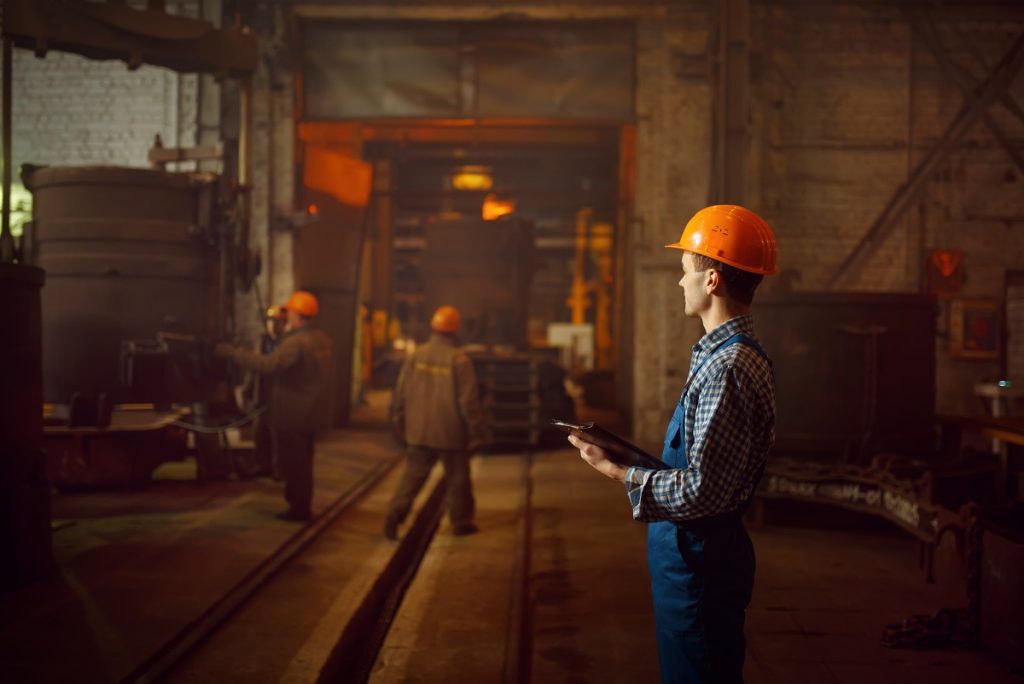
What are some methods of metal casting?
- Permanent molds
- Semi-permanent molds
- Slush casting
- Centrifugal casting
- Sand casting
- Shell molding
It escapes the notice of most, but metal casting is used by a majority of industries today that helps the world function. It’s the cheaper way to produce metal machine parts, and products of metal casting are part of our daily lives, whether we know it or not.
Metal casting is the process of pouring molten metal into an empty mold to create something new entirely. The metal would then cool down and harden in the shape of the mold it was poured into. The methods of metal casting can be grouped into two: using reusable molds and expendable molds.
REUSABLE MOLDS
These methods use molds that can be reused multiple times. Metals that are cast here are usually alloys with low melting points like zinc, aluminum, tin, and copper. This way, the mold itself won’t melt when used.
Permanent molds
As mentioned before, the cores for permanent molds must have a higher melting point than the metal being poured. But other than the alloys mention above, iron casting is also done with permanent molds. The design of these molds is often simple so that they could be reused.
To avoid damage, these molds are heated before pouring the molten metal. If you don’t, the temperature difference might cause cracks in the mold.
Semi-permanent molds
In this method, the cores might be expendable sand cores to accommodate more complex shapes. Some cores don’t need to be extracted intact after the casting process. Cores can be removed from an opening in the casting using a vibrating table. You’ll only see the characteristics of a permanent mold in the part that was cast against the metal mold.
Slush casting
This metal casting method is a way to create hollow castings without a core. You so slush casting by covering the inside of the mold with a thin layer of molten metal, like a kind of skin. You can adapt depending on how quickly the material sets. For example, if the outer layer of a material is the part that sets first, then the worker can fill the mold completely and pour out the inner part after the “skin” sets.
Centrifugal casting
The centrifugal casting method is best used for cylindrical molds like tubes and rings. The metal mold is fed into a water-cooled mold that is rotating at rapid speeds. The centrifugal force inside the mold will push the molten motel to the sides of the mold, creating a hollow tube. This method rarely creates imperfections, and when it does, it can easily be machined away.
EXPENDABLE MOLDS
People who are not knowledgeable about metal casting might think that using permanent molds is better and less costly, but expendable molds are actually better for casting ferrous metals. The stronger metals would have to be heated to a high point, and it would most likely destroy the mold in the casting process. That’s why permanent molds don’t work for ferrous metals, and cheaper expendable molds are better.
Sand Casting
Sand casting is the most common method of metal casting. It uses cores made of sand and it doesn’t have to be intact after the casting process. In fact, the cores are often vibrated away on a vibrating table, leaving only the metal product. It is efficient because sand is very cheap and easy to find. Also, the parts of the mold don’t have to come out intact after casting.
The results of sand casting have rough surface finishes, so it is better used for large rugged parts. Car engines, cast iron pans, fences, and other things are ideal.
Shell molding
This method is a form of sand casting designed for smaller tolerances. For shell molding, the sand is mixed with a certain resin. The mixture is then poured into the halves of a metal mold to create a shell after they cool down. They are then brought together. With the support of the resin, and sometimes with a flask full of sand, a very precise mold is created.
A common use for shell molding is to create cores for sand casting. The strength provided by the resin helps the sand cores keep their shape. The cores become hollow because of a method similar to slush casting. The core mold’s halves are clamped and heated. Then after being filled with resin-coated sand, the mold is baked until the wall is thick enough, and the excess is poured out. After being split, you’ll find the core inside, ready for sand casting purposes.
Key Takeaway
The different methods of metal casting are used to make parts with different functions. Whether you’re using permanent molds or sand casting methods, your product’s quality will depend on how well you’ve done it and how good your metal is.
If you’re looking for high-quality metal products, then you’re in the right place! The team behind Metal Exponents is comprised of experienced experts and engineers, ensuring that the products we produce are of the finest grade. Send us a message here for any inquiries!