4 Different Types Of Machining
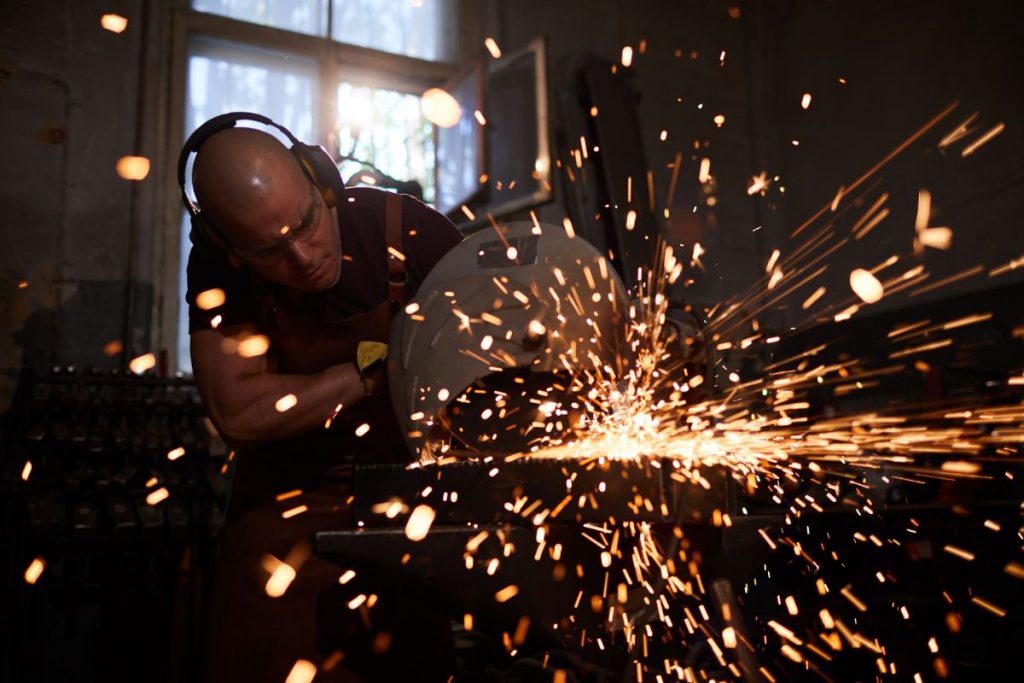
What are the different types of machining?
- Turning
- Drilling
- Milling
- Grinding
Metal fabrication is the process of cutting, shaping, or molding metal materials into a final product. It consists of creating a final product from raw or semi-finished materials instead of assembling an end product from ready-made materials. To succeed in doing that, metal fabrication involves different kinds of methods and processes. Machining is one of the ways in which fabricators can remove parts of the materials. There are a few types of machining that let them vary their methods.
Through machining, fabricators can change the raw materials into their ideal shapes or sizes. The process is typically done for metal products, but it can be used for other raw materials such as plastic, stone, wood, ceramic, and others. To convert the raw material into the final product, machining methods would cut away excess materials and will involve tools such as abrasive wheels, discs, drills, and others. This is a subtractive process that can be compared to sculpting.
If you want to know what the kinds of machining there are, keep reading as we list them below!
Turning
Turning is a machining process that uses a lathe to cut or shave down a metal material. The tool spins the workpiece rapidly and moves it towards the cutting tool which remains stationary. The process can be done manually or automatically. Manual turning requires constant human supervision throughout the process. Automatic turning is done by a computer numerical controlled (CNC) type machine to ensure precise measurements and to eliminate the need to be operated by humans.
Turning can be done on both the interior and the exterior of the material. If it’s done in the interior, it can be called “boring” and it is typically done for tubular products. On the other hand, doing it on the exterior can also be called “facing”. The cutting tool moves across the surface of the workpiece, but the lathe would need to have a fitted cross-slide.
Drilling
Drilling is the machining process that involves creating holes in the metal material. It is one of the most important and most utilized machining processes for sheet metals because most projects require fabricators to create holes to aid the assembly of the final product. A drill press is used for this process, though you can also attach some drill bits to lathes. Standard drill presses are the go-to tools for this task. However, modern advances allow workers nowadays to use computer-controlled drill presses to make more intricate holes.
Drilling is used in most projects to create preliminary holes that will later be refined through tapping, reaming, boring, and other necessary methods. Another reason is that drill bits create holes larger than their nominal size because the flexibility of the drills causes them to take an irregular route in the workpiece. The holes don’t always end up being straight or round as well.
The difference between drilling and boring is that boring is used to fix and refine the dimensions of holes instead of preliminary drilling.
Milling
Milling is another machining process that can be performed to create holes or change the shape of the material to the specifications that you need. Unlike turning, the cutting tool is rotating to remove parts of a clamped-down metal material. Traditional milling machines utilize a stationary cutting tool while the table where the material is clamped can move. Some modern machines have movable for both.
For most machine shops, the milling machine is the most flexible as it is capable to do plenty of processes such as cutting, routing, die-sinking, and rabbeting. This separates it from drilling which can only do round, cylindrical holes. Some workers consider milling as a less accurate process than turning, but modern CNC milling machines today are more accurate than worker-controlled machines.
There are two types of milling: face milling and slab milling. Slab milling uses the edges of the cutter to make cuts across the surface of the workpiece. Face milling uses the end of the cutter. Although these are the two general types, there are still some special cutters for other tasks such as ball-nose cutters.
Grinding
Grinding is a process done to improve the surface finish and tighten the tolerances of both flat and cylindrical materials. The grinders will remove small amounts of excess material from the surface of the workpiece. A few of its types are surface grinders, cylindrical grinders, centerless grinding, and double-disc grinding.
Key Takeaway
The different types of machining are helpful in the metal fabrication process to achieve the proper shape and dimensions needed for the final product. Some examples of final machined products are nuts, bolts, flanges, plaques, drill bits, automobile parts, smaller components, and many more.
If you’re in the metal fabrication industry, you would need to get some quality metal products for your next fabrication or machining project. The best place to get those products is here with us at Metal Exponents. We are the leading supplier of the finest metal products in the Philippines. Take a look at our products here, and contact us if you’re interested!