What to Ask Your Local Steel Supplier about Their Quality Processes
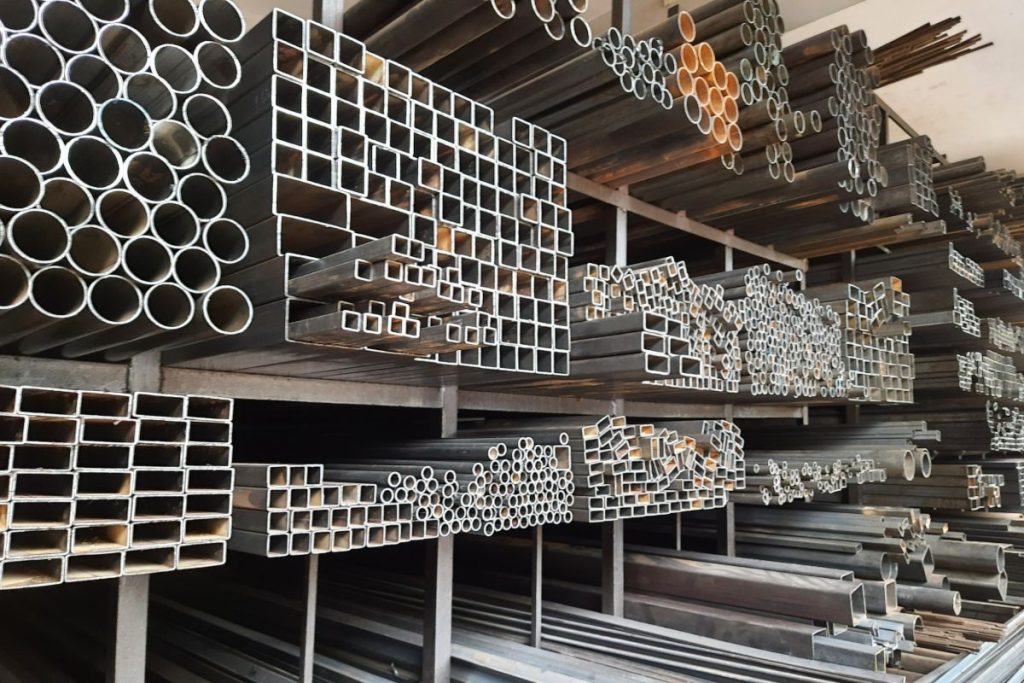
What should you ask your local steel supplier about their quality processes?
- What range of products and services do you offer?
- What quality certifications do you hold?
- What inspection and testing procedures do you follow?
- How do you ensure consistency in quality?
- Do you offer product customization?
Overview
- When sourcing steel, understanding a supplier’s quality processes is crucial to prevent structural failures and long-term safety issues.
- Key questions to ask your supplier include their range of products and services, quality certifications held, inspection and testing procedures followed, methods for ensuring consistency in quality, and whether they offer product customization.
- Asking these detailed questions upfront helps ensure reliable sourcing and protects your project from potential quality-related problems.
Choosing a local steel supplier enables you to verify quality up close when sourcing steel for your project. You need to be sure that the materials you’re getting meet industry standards and are built to last.
That’s why asking the right questions about your supplier’s quality processes is essential. From raw material sourcing to inspection protocols, understanding how your steel is produced, tested, and handled can save you from costly rework, delays, and safety risks down the line.
In this guide, we’ll walk you through what questions to ask your local steel supplier and their quality processes. This way, you can ensure that every piece of steel that goes into your project is up to the task.
What Range of Products and Services Do You Offer?
Before committing to a supplier, ask what types and grades of steel they carry and other profiles relevant to your project. If your scope involves multiple formats or additional metals, confirm if these are available to avoid the need for multiple vendors.
At Metal Exponents Inc., we offer one of the most complete steel selections in the Philippines, backed by long-standing partnerships with producers across China, Japan, Taiwan, Korea, and Europe.
From standard builds to complex requirements, our wide-ranging inventory and in-house capabilities help you secure the right materials with fewer delays.
What Quality Certifications Do You Hold?
Ask your supplier to provide proof of quality certifications like ISO or mill test to know if they adhere to strict compliance. This guarantees that your materials meet the standards you’re depending on, especially when disputes or inspections arise.
That’s why we make certification a core part of our process. At Metal Exponents Inc., every product we deliver comes with documentation that verifies quality, strength, and composition, giving clients the confidence that materials will perform as expected from day one.
What Inspection and Testing Procedures Do You Follow?
When it comes to structural integrity, visual claims of “high quality” aren’t enough. You’ll want to know exactly how your supplier verifies the performance and consistency of every batch.
Ask about their inspection process, from surface evaluations and dimensional checks to more technical assessments like tensile, hardness, or chemical composition testing.
How often are inspections conducted? Are third-party labs involved, and do they follow ASTM or ISO standards? These details can help you gauge how proactive the supplier is in preventing defects before the materials reach your site.
Understanding their quality control protocols also gives you more leverage when issues arise.
How Do You Ensure Consistency in Quality?
Consistency matters just as much as strength when it comes to steel. Ask how they maintain uniform quality across different batches, especially during multi-phase builds. Explore how they oversee production consistency, manage sourcing, and ensure follow-through beyond the first delivery.
It also helps to request references or case studies from previous clients. Their ability to repeatedly meet specs across different timelines or project scales says more than any one-time promise. Strong quality control systems should include batch traceability, documented inspections, and clear procedures for addressing issues if they arise.
Metal Exponents Inc. draws on decades of partnerships with trusted international mills, backed by a technical team that oversees quality from sourcing to shipment. With strict batch traceability and step-by-step inspection protocols, we make sure every order meets your standards from the first delivery to the last.
Do You Offer Product Customization?
When your project requires steel in specific sizes, shapes, or finishes, it’s important to know whether your supplier can accommodate those needs without delay or compromise.
Customization allows you to match material specs more closely to site needs, which helps reduce onsite adjustments, installation errors, and labor inefficiencies.
Ask how they handle non-standard requests: What types of customization are available? How long does it typically take? What kind of support do they provide during the process?
These questions help you gauge their capacity to deliver precision without bottlenecks.
Key Takeaway
By knowing what to ask a steel supplier about their quality processes, you’re better positioned to source reliably, build safely, and minimize costly surprises later on.
Ensure the success of any project with Metal Exponents. As a trusted steel supplier in the Philippines, we deliver quality materials that ensure your builds are strong and on schedule. Contact us today to learn more.