Why Sheet Metal Fabrication is Crucial for Modern Products
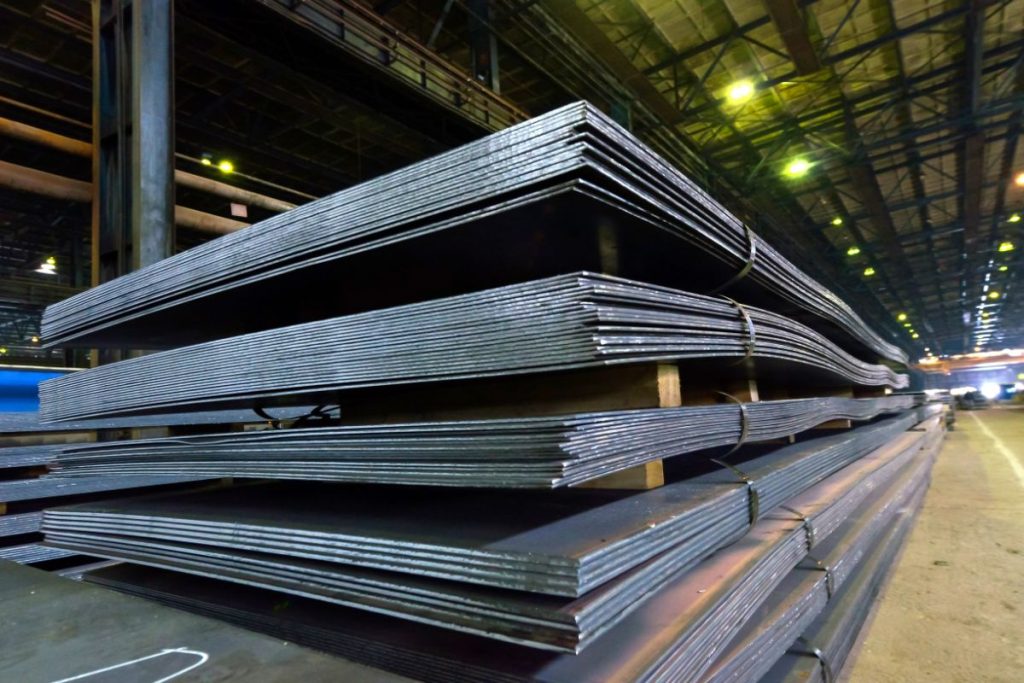
Why sheet metal fabrication is crucial for modern products?
- Offers design flexibility
- Enables cost-effective mass production
- Provides durability and corrosion resistance
- Facilitates precise manufacturing
- Supports sustainability
Overview
- This article will delve into why sheet metal fabrication remains a crucial tool for modern product development.
- By embracing sheet metal fabrication, manufacturers can achieve a balance between functionality, longevity, and environmental responsibility.
Sheet metal fabrication is a cornerstone in the manufacturing of modern products, offering unparalleled precision, efficiency, and versatility. This process involves transforming flat sheets of metal into complex structures and components, making it indispensable in the automotive, aerospace, electronics, and construction industries.
Understanding the role of sheet metal fabrication for modern products reveals how it enables the production of durable, high-quality products that meet the standards. Read on to learn more.
Offers Design Flexibility
Complex or intricate designs pose challenges for production. However, fabrication offers a remarkable degree of flexibility. This stems from the vast range of available materials, thicknesses, and dimensions. The broad spectrum allows manufacturers to create intricate components that were previously impossible with conventional methods.
Furthermore, modern computer-aided design (CAD) software empowers designers to manipulate sheet metal virtually. This allows for precise adjustments to product size and form within the program, granting even greater design freedom.
Beyond shaping, it can be bent, sliced, and perforated with high accuracy, enabling the creation of truly unique and intricate designs. This flexibility translates to a wider range of customization options for businesses, all without compromising the inherent durability of metal.
Enables Cost-effective Mass Production
The process minimizes material waste unlike machining or casting, which often involve removing large chunks of material. Precise cutting and forming techniques ensure minimal waste, directly translating to lower production costs per unit. This benefit becomes even more pronounced when dealing with large quantities.
Once the initial setup and tooling for a specific product are established, production can be easily ramped up to meet high demand. This allows manufacturers to respond to market fluctuations efficiently without significant additional investment.
Items such as refrigerators, washing machines, and microwaves often have their external casings and internal components crafted from sheet metal. The techniques used in sheet metal fabrication ensure these appliances are durable, aesthetically pleasing, and cost-effective to produce.
Provides Durability and Corrosion Resistance
The metal’s true strength lies in its ability to withstand physical stress and impact. This makes it the perfect choice for products destined for demanding environments. It offers superior resistance to bending, warping, or cracking under pressure compared to some plastics or composites.
It is often enhanced with protective finishes or coatings and boasts exceptional resistance to corrosion. This is crucial for products exposed to moisture, humidity, or harsh chemicals, where corrosion can quickly compromise a product’s structural integrity and functionality.
For instance, industrial machinery such as heavy-duty manufacturing equipment, construction tools, and mining implements are typically made from metal due to their need to endure intense physical stress. This ensures longevity, reliability, and optimal performance even in the most challenging conditions.
Facilitates Precise Manufacturing
Modern products across diverse industries, from automobiles and airplanes to medical devices and electronics, require tight tolerances and precise dimensions. Sheet metal fabrication offers manufacturers a reliable solution for achieving this level of precision.
In the medical field, devices such as surgical instruments, implantable devices, and diagnostic equipment are often made from sheet metal to meet stringent hygiene and accuracy standards.
On the other hand, electronics from this fabrication by producing enclosures, frames, and chassis for computers, smartphones, and other consumer electronics.
The process utilizes a variety of techniques, including stamping, bending, and computer-controlled cutting (CNC) with automated machinery. This automation guarantees consistent and repeatable production.
Supports Sustainability
Sheet metal is one of the most recycled materials globally. This reduces the need for virgin material extraction, lowers energy consumption associated with production, and minimizes landfill waste.
Furthermore, its renowned strength and durability translate to products that can last for decades with proper maintenance. The products have a smaller environmental impact over their entire lifespan because they require fewer replacements.
Beyond sustainability, its lightweight nature offers additional environmental benefits. In applications like the automotive industry, lighter car parts fabricated from this can contribute to improved fuel efficiency. This results in reduced greenhouse gas emissions during a product’s use phase, making it a win for both the environment and your bottom line.
Key Takeaway
By embracing the importance of sheet metal fabrication for modern products, manufacturers can achieve a balance between functionality, longevity, and environmental responsibility, paving the way for a future filled with innovative and sustainable products.
As the leading supplier of imported steel products and parts in the Philippines, Metal Exponents Inc. is your one-stop shop for all your construction needs. Inquire now to get started on your next project and let our team of specialists guide you through the process.