What Are the Differences Between Metal Fabrication and Welding?
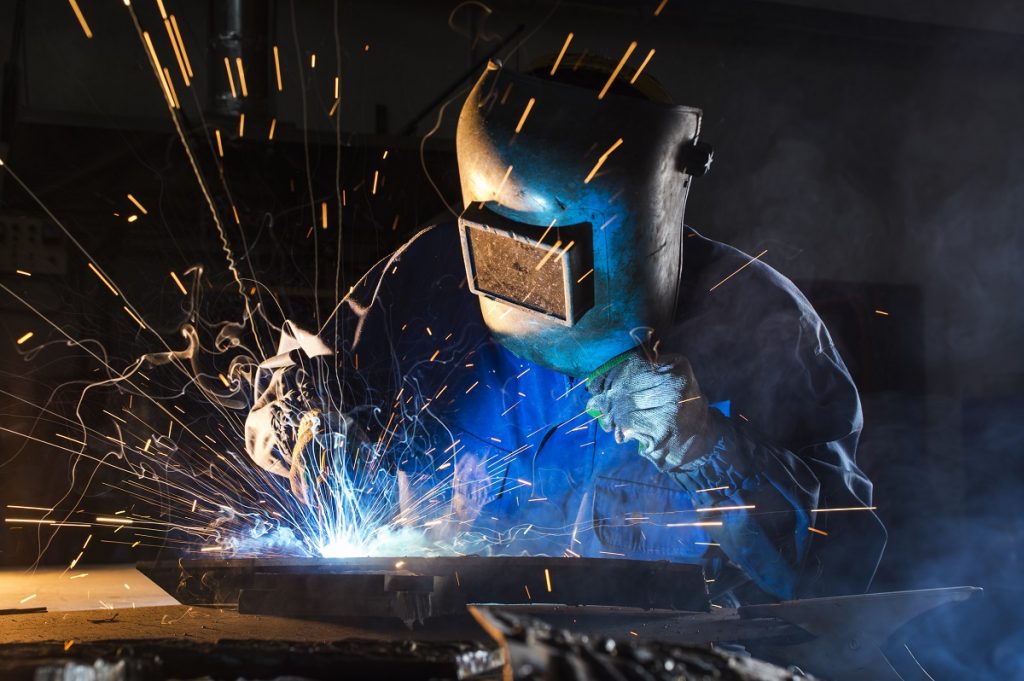
What are the differences between metal fabrication and welding?
- Tools used
- Processes involved
Many people use the terms “metal fabrication” and “welding” interchangeably, however, there are stark differences between the two. While welding refers to the process of joining two materials together — be it metal to metal, metal to plastic, metal to wood —, fabrication involves the creation of a part or equipment entirely out of metal. In metal fabrication vs welding, you’ll discover that the variation lies not just in the definition of the two, but also in the tools and processes involved.
What is Metal Fabrication?
Metal fabrication starts with the raw material procurement to produce the type of metal needed for the job. For example, when it comes to aluminum metal fabrication, aluminum production facilities will start by conducting geographical assessments on bauxite ore reserves. The ores will be extracted from the surface using heavy machinery, transported to a refinery plant to extract the alumina, then cast into ingots, billets, and other pre-finished aluminum goods.
The metal fabrication phase begins when these pre-finished parts are manipulated into sheets, coils, or wires. The fabricator will conduct a number of fabricating methods that may include cutting, welding, forming, burning, machining, dishing, and other specialized techniques as necessary.
A metal fabrication project can come out in different ways — from simple hand railings, heavy machinery, cutting tools, structural sections, screws, nuts, bolts, and other such assembly parts and fittings.
What is Welding?
As mentioned before, the main idea of any welding process is to fuse two materials together through a welding machine. Welding can be done either with or without the use of a filler material — can be done with an alloy or non-alloy. Designed to be heated, liquefied, and molted to flow between the gaps of the two materials to be combined, the filler metal creates a solder-like joint, effectively fusing the two together.
Like metal fabrication, welding is classified according to the types of techniques and sub-processes involved. One technique, for example, metal gas inert (MIG) uses wires to combine two or more metals together. Stick welding, on the other hand, melts a wire electrode to add strength to the combination.
Tools Used
Many of the tools used in metal fabrication can be used for welding, but not all welding tools can be adapted for metal fabrication. This is because the processes require specific instruments.
Currently, the most common instruments for metal manufacturing and fabrication will depend on the method. For cutting, working tools can be classified into the following:
- Cutting saws
- Angle grinders
- Shears
- Drill bits
- Deburring tools
- Rolling equipment
- Broaching equipment
- Gear shaping equipment
- Hobbing machine
The success of any welding project is dependent on the operator being aware of safety measures and having the skills needed to get the project done. All welders will wear typical safety equipment such as welding gloves, earplugs, respirators, and the like. During the welding itself, they will also make use of the tools listed below:
- Welding clamp
- Sheet metal gauge
- Electrode (filler metal)
- Angle grinders
- Metal brush
- Flint striker
- C-clamps
- Metal file
Despite these differences, it’s crucial that each metal fabrication or welding project be organized and well-managed. Any surface imperfections spotted on the final product will have to be smoothed out by some of these tools for successful outcomes.
Processes Involved
As previously discussed, fabrication is a broad term that encompasses both simple and complex forms of changing the appearance of metals. Basic processes may include cutting, stamping, machining, and punching. The more complex techniques, on the other hand, require specialized machinery to achieve acceptable tolerances of metal fabrication. Here’s a brief description of some of them:
- Cutting – Sheets of metal are simply cut and divided into different sections, ranging from large halves to smaller cuts. Most of the time, cutting is done on freshly cold/hot-rolled sheet metal and is yet to take form.
- Folding – A metal surface is bent at an angle. This is considered complicated since not all metals will be ductile enough to be easily manipulated at a specific angle, blunt or otherwise. Folding may only be possible in high-tech facilities equipped with the latest machining equipment due to the complexity of the process.
- Stamping – Metal fabrication will often involve the utility of die equipment that can raise or lower a certain portion of the material. Unlike punching, where a piece of the metal will be separated from the larger part, stamping intends to only create a dent on the material’s surface.
Although the industry conducts a number of welding processes, these can be classified according to the most common four types namely Gas Metal Arc Welding (GMAW), Gas Tungsten Arc Welding (GTAW), Flux Cored Arc Welding (FCAW), Shield Metal Arc Welding/Stick Welding (SMAW)
- GMAW – An electric arc is created between a consumable MIG wire and the work piece. A molten metal puddle is formed, which joins the two materials together.
- SMAW – Considered as the simplest welding technique which uses a constant electric arc current that flows through an electrode. This is used by such industries as shipyard building, pipelines, construction sites, metal repairs, and the like.
- GTAW – An electrode made out of tungsten delivers the electric current to the weld pool. GTAW is relatively complex and should be done only by an experienced welder.
- FCAW – Flux cored welding can either be semi or fully automatic that depends on a continuously fed flux electrode. The welding operation is shielded by a gas to prevent external contamination.
Key Takeaway
When discussing metal fabrication vs welding, it’s easy to conflate the two techniques. Both require specific tools and equipment to achieve angled bends, cuts, lacerations, holes, and joints. However, the similarities end when looking into the kinds of processes done to complete a certain fabrication or welding project.
Understanding the nuances between welding and fabrication is crucial for any manufacturing setting. When you’re aware of the distinction, you can choose the correct method and materials needed for the job.