A Guide to the Different Types of Metal Finishes
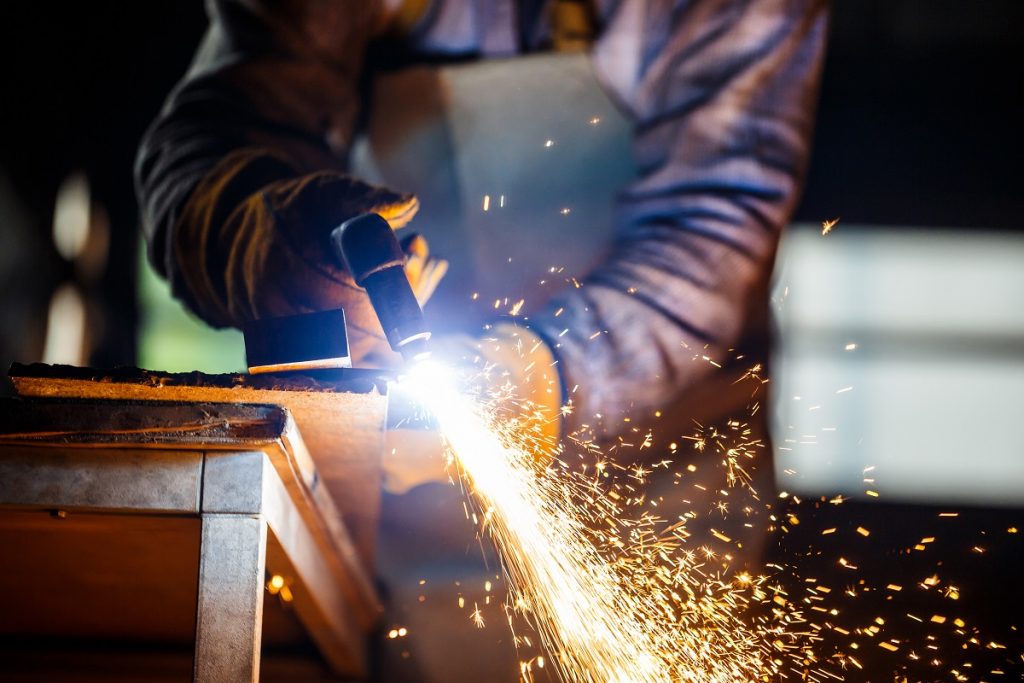
What are the different types of metal finishes?
- Plating
- Polishing
- Blasting
- Passivation
- Powder coating
Simply put, metal finishing describes a process of applying a type of layer of coating or substrate to the surface of a metal. It can also refer to an industrial undertaking that assists in cleaning the metal surface in order to prepare it for further production. Many types of metal finishes accommodate a combination of electrical, chemical, and mechanical processes to achieve the desired result. Continue reading to learn more.
Plating
Though there are many sub-categories of metal plating, the benefits of subjecting a metal to this process are consistent all throughout. Metal plating improves the corrosion-resistant capabilities of the metal, toughens the surface, and diminishes the level of friction once the metal comes into contact with other material. Both non-ferrous and non-ferrous metals are used in plating, like gold, zinc, tin, copper, or chromium.
Electroplating is arguably the most common form of plating, and it typically involves a metal deposition process in which the metal to be used for plating is dissolved and transferred onto the surface of the metal specimen. Generally, there are four main components that are involved in electroplating, like the cathode, anode, an electrolytic solution, and a constant current. The anode refers to the metal that will plate the cathode or the specimen. This entire process takes place in the solution where both the cathode and anode are submerged and serves as the medium for the current to pass.
Polishing
Like all metal finishing, polishing involves the removal of imperfections on the metal surface. Depending on the state and condition of the metal, polishing makes use of different abrasives that may be classified as coated, bonded, or loose media. Coarser or rougher abrasives are used in the primary process to smoothen out the larger and more stubborn deformities. After, finer abrasives are utilized for further polishing.
Aside from the condition of the metal, the type of metal also determines which abrasives will be part of the polishing equipment. This is largely dependent on the tensile strength, which measures the maximum load that the material is able to withstand before breakage. Low-tensile strength metals like copper, brass, or aluminum make use of silicon oxide abrasives. On the contrary, high-tensile strength metals like iron and carbon require grey or white aluminum oxides. These abrasives are used in combination with polishing materials like cloth, cotton, rubber, and the like.
Blasting
Also commonly referred to as sandblasting or abrasive blasting, this process involves the use of a high-powered blasting component or machinery that launches a stream of abrasives. Like polishing, blasting smoothens out the rough surfaces in order to remove the defects on the metal. Unlike polishing, however, milder abrasives are preferred over coarser ones and the resulting polish is more matte-like in texture.
Other subcategories involved in blasting, like shot peening, improve upon many properties of the metal, such as its cracking and fatigue resistance, as well as stress corrosion. The compression force produced by the peening or striking mechanism, creates numerous concave formations on the surface of the metal, thereby improving the types of resistances and resulting in a stronger, yet lighter-weight specimen.
Passivation
As you may already know, ferrous metals (metals that have a high iron content) are more prone to corrosions and forms of oxidation. Due to environmental stresses, rusting and other forms of corrosion may occur on these metals. To remediate this, metal finishing techniques like passivation are done on stainless steel in order to prevent rusting once the metal has undergone exposure.
Passivation is in some ways similar to electroplating, in that it increases the alloy’s corrosion resistance. However, it differs in the method and material. Instead of the transfer of metal ions, passivation involves the removal of freely-flowing iron from the surface of the metal. This greatly reduces the rate at which the specimen will undergo a chemical reaction. With the removal of free iron, other substances take the fore. For example, low iron content means that nickel or chromium may be left behind on the treated surface.
Powder coating
Powder coating is another metal finishing process that is used to protect both metals and nonmetals. The process involves methods that are similar to spray painting, but with the use of different additives, curing agents, extenders, and pigments.
In powder coating, resins or thermoplastics are applied in a targeted and uniform fashion onto the metal surface. Once the material has been left to settle, this technique produces an evenly-applied coating that greatly increases the material’s durability, quality of finish, and damage resistance. Three stages are usually involved in the powder coating process, namely surface preparation, application, and curing. Applications of the coating material can be achieved through electrostatic deposition or through fluid-dipping.
Key Takeaway
There exists a range of applications and techniques to improve on the properties of a metal or alloy. Some techniques like polishing and powder coating are more widespread among decorative uses, while some have a more functional aspect to them — particularly with passivation, sandblasting, and plating.
The appropriate metal finishing process should be applied with respect to the specimen involved. With this idea in mind, coupled with the use of the right components, manufacturers are able to take advantage of metal finishing as part of their metal fabrication practices.