Press Brake Vs Roll Form: The Different Factors
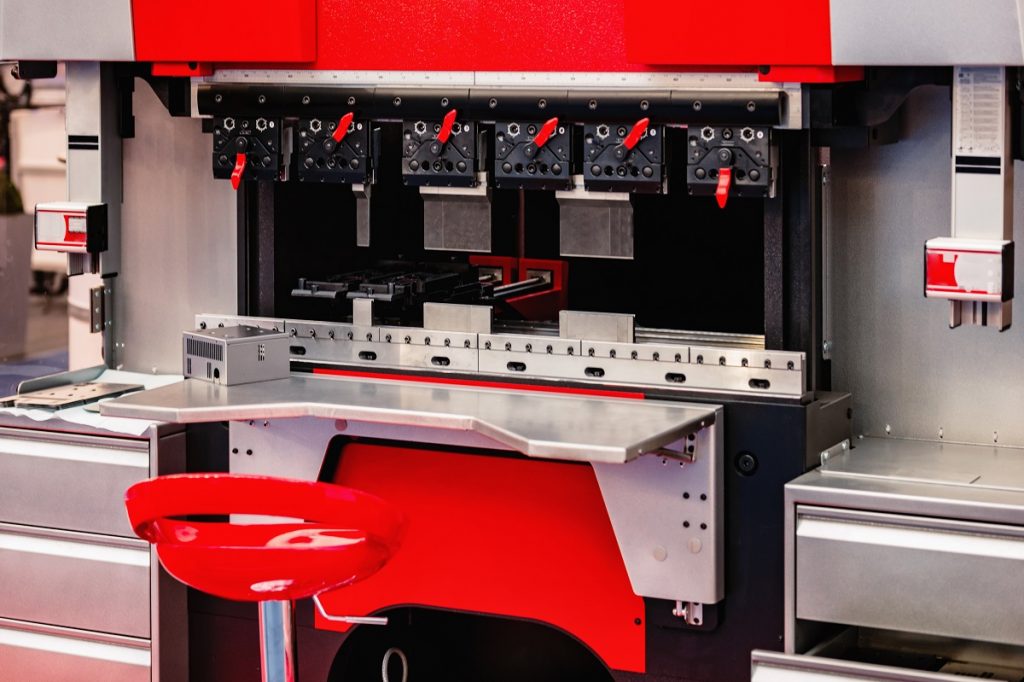
What are factors to consider when choosing press brake vs roll form?
- Process
- Length
- Materials used
- Fabrication design
- Tooling costs
The fabrication method you select for your metalworking venture usually comes down to what method can provide quality results while saving you time and costs. In this situation, two metal fabrication techniques can come to mind: press braking and roll forming. When weighing your decision between using a press brake vs a roll form, there are a few factors to think about. In this article, we review the important aspects that should be taken into consideration before deciding on your sheet metal fabrication method.
Process
The first thing to examine is the differences in each process. In press braking, metal deformation occurs using a machine that aligns a piece of sheet metal along an axis. The machine then uses a pressing tool (a.k.a. a press brake) to clamp the sheet metal between a punch and a die set for prearranged bending.
This process, if done by experienced workers, can ensure a highly precise metal bend for several types of parts. The press braking can form a variety of shapes. Some of the most common are: V bottom, channel, 90° rib form, closing, offset, and others.
Roll forming on the other hand is a type of metal bending that uses continuous rolling of long sheets of metal. The sheet metal strip passes through a set of rolls mounted on two stands. Each set of rolls makes an incremental part of the bend until the intended profile is achieved. This simple process can produce complex shapes.
Length
The length of your sheet metal is an essential factor — some sizes may not be compatible with certain techniques or machines. Press braking is not suited for manufacturing big sheet metal parts. This is because the press brake tools and dies aren’t designed to accommodate large pieces. Press braking material needs to be split and cut to length before being put into a press brake. Furthermore, these pieces require secondary operations to form the intended large piece after being worked by a press brake. These extra steps add to cost and can increase product weight.
In contrast, this extra work is not needed with the roll forming method. Long parts of sheet metal can be added directly into the roll forming line. Long pieces can be made without the need for prior working or secondary operations. Thus, less time and effort are needed, and less scrap is produced. Production of larger sheet metals is more efficient and less wasteful with the roll forming method.
Materials used
The materials you use are also another critical factor to consider. Material selection will impact cost control and product design, which then affects which fabrication process best fits. Certain processes also perform better when working with particular materials.
Both roll forming and press braking work best with lighter materials. High-strength metals can be difficult to work with using these two techniques. This is due to the challenges of controlling spring back, which is the geometric changes that can occur to a pressed or formed metal when the piece is released from the force of the forming tool.
It’s still technically possible to work with high-strength metals, as there are techniques to compensate for spring back. These techniques are overbending, where the metal is bent past the desired angle to adjust for spring back; and re-bending, where the metal is simply bent repeatedly until the desired shape is achieved. However, these techniques need extra labor, increasing expenses. So in any case, we recommend you opt for durable, light metals for both press braking and roll forming.
Fabrication design
Your intended fabrication design will also affect the compatibility of either method. Press braking and roll forming use different processes, and each process differs on the time needed to complete complex bends and shapes.
For instance, press braking can only handle a certain amount of bends before efficiency and viability become an issue. Moreover, each bend requires a separate pass in the machine. Because of this one-hit process, more complex forms take longer to create. This can slow down production and increase labor costs.
Conversely, roll forming can form complex shapes in a single pass, which simplifies production time. A roll-form machine can create almost any linear shape you desire. This way, multiple tooling steps are eliminated during the fabrication process. As a result, despite the complexity of design, you could reduce production and labor costs with this method.
Tooling costs
Tooling costs of both press braking and roll-forming are generally pretty similar. However, there can be some differences depending on certain specifications of the project. The general rule of thumb for roll forming is: The larger the product volume, the tooling cost per piece will be lower. If the run is short, or volume is low, then press brake tooling will cost less per piece than roll forming. You must first determine your metal project’s volume before you can accurately compare the tooling costs of both methods.
Key Takeaway
For your decision on using a press brake vs a roll form, weigh each of these factors carefully. Both processes have distinct advantages and disadvantages you need to take into account. This decision will be easier to make if you align with a reliable fabrication partner that can help you design and execute your metal products.
Metal Exponent’s engineers are trained to help you to achieve the best quality for your custom sheet metal forms. Message us today to get suggestions for your sheet metal application needs. From design to materials and more, Metal Exponents has the answer to your custom sheet metal inquiries.