9 Types Of Metal Forming Processes
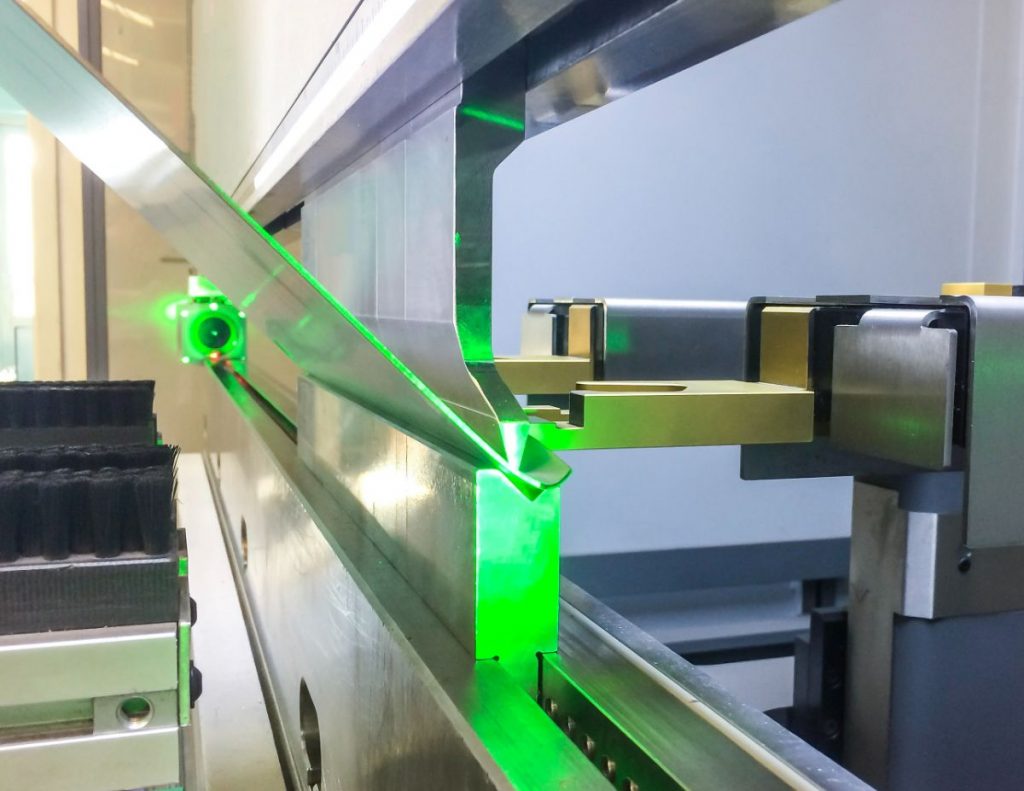
What are the types of metal forming processes?
- Bending
- Stretching
- Deep Drawing
- Roll Forming
- Extrusion
- Punching
- Stamping
- Ironing
- Hydroforming
Metal forming is a part of the metal fabrication process and is used to create structural parts or complex pieces out of metal sheets and tubing. It’s an essential procedure for a wide variety of products — without it, our society would come to a grinding halt. Most metal items you see and use today are created through different metal forming processes. From heavy scaffolding to simple steel benches, everything goes through metal forming at one point or another. And, there are several types of metal forming processes that are used today, each one offering different purposes and benefits to manufacturers.
What is metal forming?
Metal forming processes are used to apply stress, compression, or both upon a piece of metal. Metal forming may also be used to cut, drill, fold or bend the workpiece. This is done for plastic deformation, i.e., to geometrically change the metal piece to be used as a component or part in the next manufacturing step.
Each metal forming process takes a significant amount of practice to master. The tools and machines used for each process also take skill to operate, are usually expensive, and take up a lot of working space.
During any metal forming process, the metal does not lose mass — it only changes its form. To ensure success, metal forming processes must strike a balance between the strength and formability of the metal. This is key to preventing defects, such as splits and creases.
A few of the most commonly used metal forming techniques are:
Bending
This is a flexible metal forming process. It typically utilizes a brake press, but can also be performed by similar press machines. In this process, a metal sheet is placed over a die block, which punch-presses the sheet. The die does not punch a hole in the sheet, but rather uses a bending force to shape the metal against the die. Bending can be further categorized as other processes, such as press braking, rotary bending, and roll bending (depending on what kind of die is used).
Stretching
Stretching is a metal forming process that stretches and bends a metal piece simultaneously, through the help of a die. This is used to form complex or contoured metal components. It is also used to shape large-format metal pieces that need significant and accurate radius bends while keeping a smooth surface.
Deep Drawing
Deep drawing is another widely used metal forming process. With a deep drawing, a metal sheet is clamped and placed over a cavity-shaped die. It is then punched down, which causes it to be “drawn” through the cavity — hence the name. The result is the metal sheet taking the shape of the die, which is usually cup- or box-shaped. Deep drawing is generally used to make complex metal components or intricate designs.
Roll Forming
Roll forming shapes metal workpieces via successive sets of rollers. The metal piece is conveyed through the roll forming machine, where several sets of rollers continuously work against its surface. These form and bend the metal into a desired cross-section. Roll forming is performed multiple times, gradually forming the metal piece until the correct cross-section is achieved. It is typically used to produce pieces with long lengths and is suitable for long production runs.
Extrusion
Extrusion is another metal forming process that forces a metal workpiece through a die. This creates the desired cross-section. But, this process is slightly different from the others. When performing extrusion, the metal piece is heated at high temperatures to make it more pliable before being pressed against the die. The heated metal is so heated that it becomes almost fluid-like. The die itself also has an opening, where the heated metal flows through after being pressed.
Punching
This process utilizes a punch and a set of dies to create holes in a piece of metal. The punching process involves placing the metal under the die, and a drill machine is used for the die to punch through the piece. Punching has two sub-categories, depending on how the process is applied. Generally, punching is used to create holes to fasten latches or other components. In other cases, punching is used to extract a smaller piece from the main body for components — which is called blanking.
Stamping
Punching is not the only process that utilizes a punch and drilling mechanism to force a metal piece against the die. However, unlike punching, stamping is used only to raise selected portions of the metal piece — without penetrating through the surface. So, stamping is somewhat similar to relief carving for materials like wood and marble.
Ironing
To achieve a uniform thickness across the entire metal section, ironing is typically performed. This process can be performed in two ways. The first is through a set of rollers, where the metal piece gradually becomes uniform. The second is through a punch machine, which forces the metal between two dies to create the same effect.
Hydroforming
One less-known metal forming process — yet becoming increasingly used in the manufacturing industry — is hydroforming. Similar to deep drawing, hydroforming forces metal pieces against a die to stretch or draw it out. The difference between the two processes is that deep drawing does its forming gradually. On the other hand, hydroforming can complete the same in just one step.
Key Takeaway
Metal forming is a broad manufacturing process that encompasses several techniques, equipment, and applications. There are many different types of metal forming processes, with each playing an important role in reshaping raw metal into a finished component or product.
At Metal Exponents, our custom metal fabrication processes utilize many metal forming processes. Our team is specially equipped with extensive training and quality machinery to perform such tasks. To learn more about our services and products, message us today!