Metal Fabrication Mistakes To Avoid
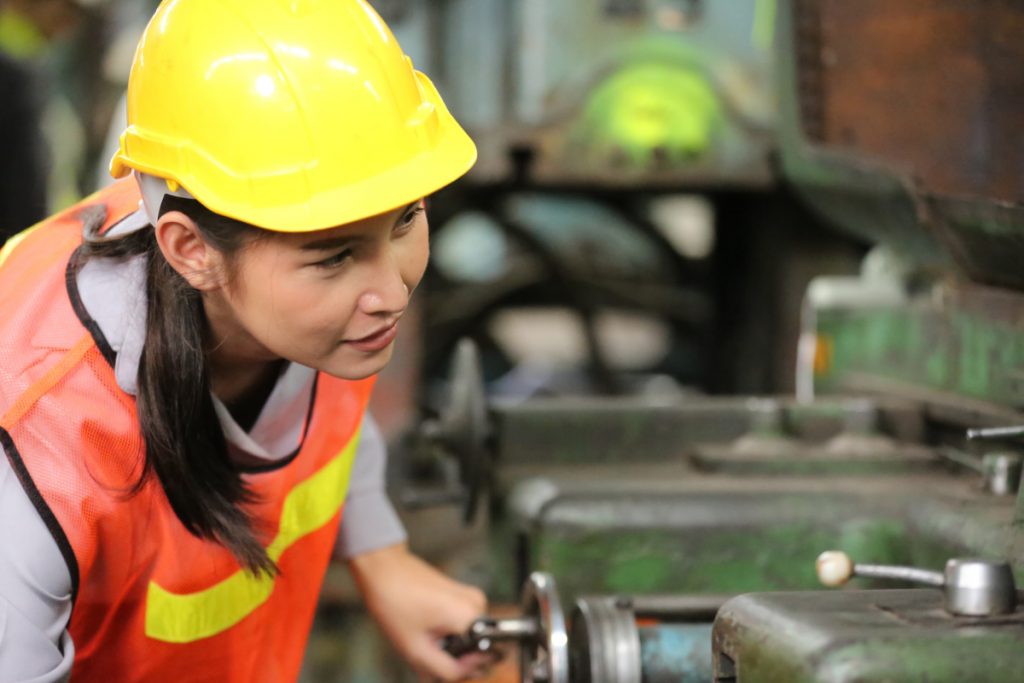
What are some metal fabrication mistakes to avoid?
- Making assumptions
- Improper storage
- Wrong use of materials
- Incorrect arc striking
- Scheduling issues
Because it involves shaping metals, metal fabrication is a very detailed industry. Precision and accuracy are both important, and mistakes can be costly. To avoid making these metal fabrication mistakes, you need to be aware of what they are. Those who are new to the industry are susceptible to making these mistakes, but even veterans can sometimes slip up as well. Either way, the best way to avoid them is to know about them.
The process of metal fabrication consists of several steps, some manpower, and heavy equipment. Any mistakes that are made can also be safety issues that affect workers, and not just more expenses or less productivity. The well-being of the workers makes the importance of avoiding the following mistakes double.
Here are some of the most common mistakes in metal fabrication that you should avoid.
Making Assumptions
As mentioned earlier, details are very important in the metal fabrication industry. The output will become parts of a machine and will have many applications in a range of industries. The quality of the products will dictate how well the equipment will perform in their various niches. That’s why all specifications and measurements should be followed precisely.
For most instances, even the slightest miscalculation can greatly affect the performance of the final product. If there is a missing measurement, never make assumptions about it and simply ask the client to make sure.
Improper Storage
Material storage can be easily taken for granted in metal fabrication. Some less careful workers might overlook some things which would ultimately lead to more expenses and a lower quality product. The best example of improper storage is fillers used for welding. Filler metals are ferrous, meaning they have iron in them, making them susceptible to corrosion. Storing them in a moist environment will lead to rust, and rust on filler material will lead to defective welding. You would need to use binders which will up the costs of the project.
Wrong Use Of Materials
Metal fabrication facilities make two common mistakes: using only cheap materials without understanding them or only using the strongest material. Both of these could compromise the project as they will cause problems down the line. While it’s understandable to choose cheap and light materials to minimize costs, not knowing how to properly handle them will be disadvantageous. It could affect both productivity and output quality.
On the other hand, don’t be tempted to always use the strongest material there is. Some processes would be easier and would work better with more flexible or lighter material. Using a material that’s stronger than what’s needed would also be harder to manipulate and fabricate. If the design has complicated shapes and sizes, your efforts might need to be doubled. In essence, you should be more knowledgeable about the materials you use and learn to find the right ones for your project.
Incorrect Arc Striking
Arc striking is how welders produce heat for the weld. It melts the filler material and attaches to the metal. If the arc is not labeled correctly, it could be heated too much and damage the metal itself. This could lead to a large waste of materials. Also, if the welder accidentally strikes it somewhere else, like a piece of scrap or a different piece of metal, it could stick there if the welder doesn’t pull away quickly enough. You need to pull away before the arc sticks to the weld plate, but pulling away too far will also eliminate the arc. To avoid this, make sure you only strike the arc at the exact stops needed.
Scheduling Issues
Some metal fabrication facilities tend to overbook themselves, especially when they’re in need of more business. There are many factors that go into metal fabrication, and scheduling them all properly is essential. Consider the time it takes for materials to arrive or to settle, for each process to finish, and everything else that goes into your project.
Avoid rushing a project as it can greatly deteriorate the quality of the finished product. Rushing projects can also result in physical injury and loss of material. It’s also important to avoid booking too many projects at once — stick with the amount that you can handle.
Key Takeaway
These metal fabrication mistakes are more common than you might think, so if you want to survive in the industry, keep them in mind and do your best to avoid them. There are still plenty of other mistakes that you may make, but that’s normal. Just make sure you take note, learn from them, and carry on.
Before any metal fabrication project, you first need high-quality metal products. To find that, look for the most reliable brand that supplies metal in the country: Metal Exponents! We supply the finest steel to our clients from our partners all over Asia. You can take a look at our products here, and contact us anytime if you’re interested!