7 Common Welding Defects and How You Can Avoid Them
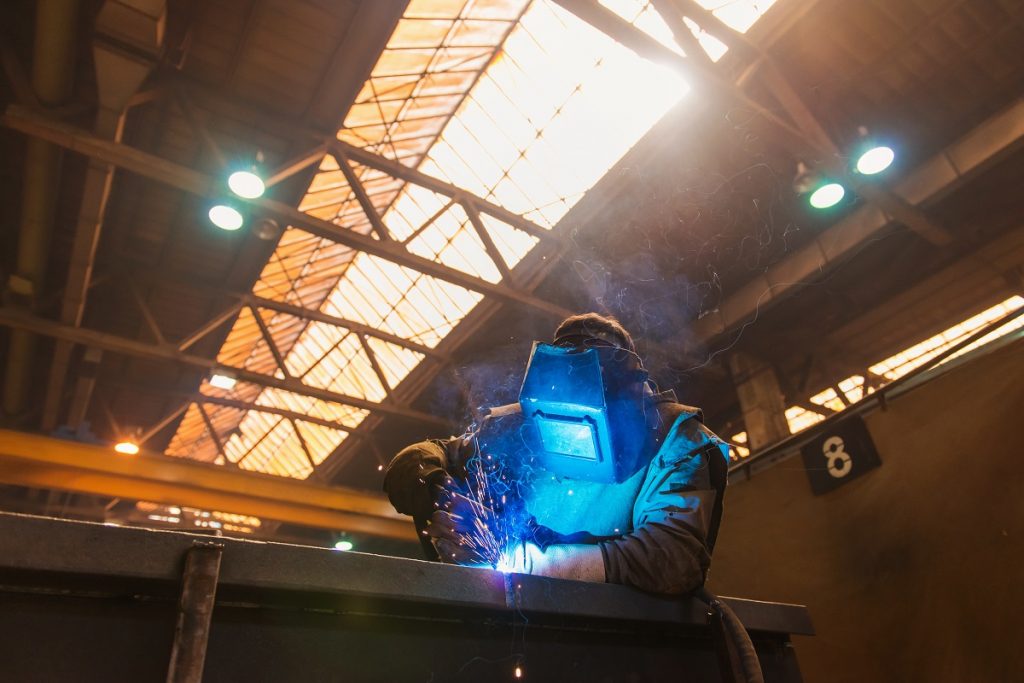
How can you avoid these common welding defects?
- Weld Crack
- Undercut
- Porosity
- Spatter
- Slag inclusion
- Incomplete fusion
- Incomplete penetration
Welders train and study a lot before being able to do it in a professional setting. But no matter how much we train, people will still make mistakes. There is room for tolerance when it comes to engineering, but if the safety of people is at stake, some mistakes cannot be allowed to happen. This means that learning how to avoid welding defects should always be part of a welder’s expertise.
Listed below are ten of the most common welding defects. Read on to learn how to avoid each of them.
Weld Crack
The weld crack is one of the most dangerous defects on this list. These cracks may show up at the surface of the weld or other heat-affected areas. They can be classified into cold cracks, hot cracks, or crater cracks. Cracks can be caused by several factors such as using unsuitable materials, contraction of the metal, contaminated base metal, and growth of grains.
To avoid these defects, the welder should use suitable materials, preheat the weld, clean the metal, give decent cooling, and ensure that the crack is filled properly. Using hydrogen while welding ferrous materials will cause cracks, so use something more suitable. When you preheat the weld and slow down the cooling, there are fewer chances for a crack to appear. Not filling them properly will surely cause cracks, as anyone might expect.
Undercut
An undercut is a groove or depression at the base of the weld toe. This happens when the metal around the weld melts away from it. The workpiece would then be weakened by this defect.
The quickest way to avoid this is by reducing the voltage and the welding speed. High current and fast travel speed of the electrode are common causes of this defect. Similarly, reducing the size of the electrode might help as well. It would not hurt to always double-check if you’re using the proper welding materials. Being cautious will always be a good decision.
Porosity
When there is air trapped underneath the weld, small bubbles form on the surface. This is called porosity. It can be caused by a number of things such as the electrode not being well-coated or by contaminated metals.
To avoid porous welds, always make sure that your working environment is clean. Contaminants from the environment entering the weld zone will cause porosity of the weld. Even moisture in the area, since it will evaporate, should be avoided. Cleaning the metal will prevent this. Also, the electrode deoxidant cannot do its job properly if there is not enough. Make sure you coat the electrode properly to avoid this welding defect.
Spatter
There are instances when small, molten metal particles are thrown from the arc during welding and get stuck on the metal. This defect is called spatter. It can also be caused by using a contaminated metal. But the most common causes are the length of the arc and the wrong polarity.
The first step to preventing spatter is to keep the metal and the environment clean. If spatter is a common defect, then try decreasing the length of the arc and adding more angle to the electrode. Using the wrong polarity could also cause spatter. Make sure to check the current and determine the polarity of the electrode to avoid this welding defect.
Slag Inclusion
Slag is a visible welding defect that significantly weakens the joint and the metal structure. If you see slag on the weld, then maybe the current density was too low or the welding speed was too fast. It can also be caused by the angle of the electrode or by the previous welding.
As with any defect, proper cleaning of the metal, especially the edges in this case, should help you avoid slag inclusion. Using the right current density and the proper electrode angle would also avoid this welding defect.
Incomplete fusion
This defect is just as it sounds. The two metals are not properly fused together, meaning there’s a gap that’s not filled with molten metal. In a metal’s cross-section, an incomplete fusion could be visible.
Being unable to fuse the metals is important for welding. Incomplete fusion can be caused by using too low of heat input, incorrect angle of the electrode or the joint, or too fast welding speed. Making sure that everything is properly placed, measured, and prepared would avoid this welding defect. Keep the heat at the right input, the electrode and joint at the right angle, and the travel of the electrode at the right speed.
Incomplete penetration
Proper penetration means that the electrode reaches from the upper surface of the base plate to the full extent of the weld nugget. Without proper penetration, a gap is left at the base, unfilled with molten metal.
Much like incomplete fusion, a proper welding technique would prevent this defect from happening. The right arc travel speed, welding current, angle, and positioning of both the joint and electrode should be observed. This defect could also be caused by a small diameter electrode.
Key Takeaway
Each defect has its own causes that might be avoided on its own. But the real trick on how to avoid welding defects is to be responsible with the job and use proper techniques. This would ensure the best possible results for your welding job.
A prerequisite to a good welding job is good quality steel. As the leading steel supplier in the Philippines, we can provide good steel for any welding or construction project there is. If you’re interested, don’t hesitate to contact us now!