9 Ways to Improve Welding Quality
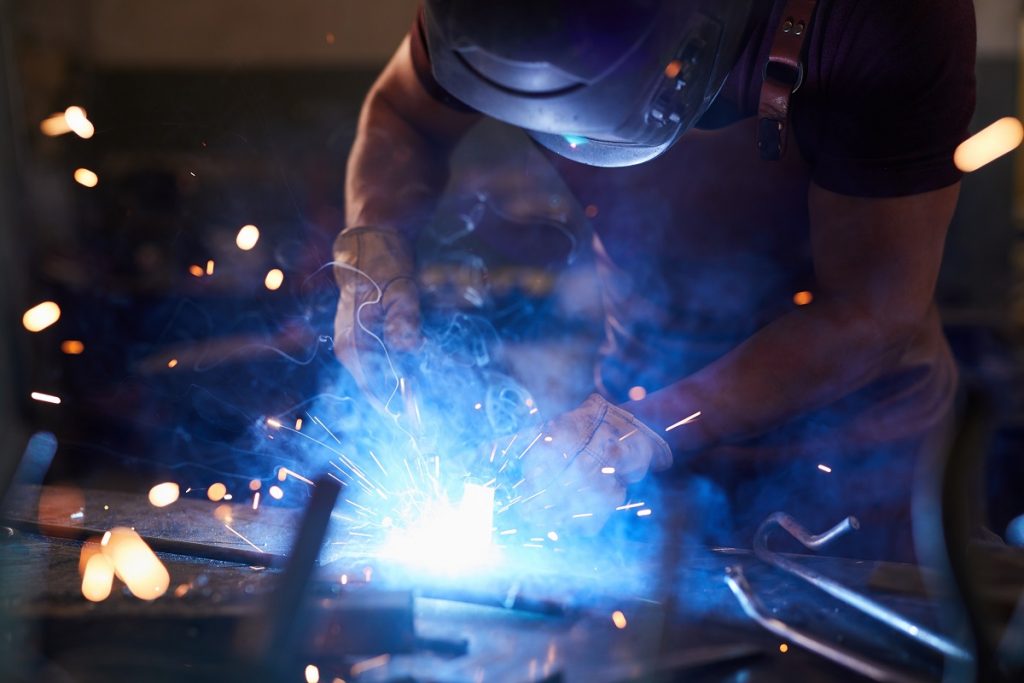
What are some ways to improve welding quality?
- Always clean
- Find a good ground
- Choose the right gas
- Use both hands
- Pace yourself
- Listen
- Match all your equipment
- Use the proper method
- Pay attention to your bead
Sometimes, welders, especially beginners, have trouble producing high-quality beads. Their output ends up porous or cracking or any of the many possible defects. It will affect the strength of the joint, the integrity of the structure, and the welder’s confidence in his skill. While many factors could contribute to defects, there are also many ways to improve welding quality. Read on to learn more!
Always clean
The most common cause of welding defects is contaminants on the material. These are any kinds of dirt that will interfere with the welding process. Dust, grease, rust, and even paint can all affect the quality of your weld.
You should never skip the first step: clean your material and workspace. This crucial step would eliminate contaminants as a factor for your weld quality.
Find a good ground
For your welding arc to function properly, you need to establish a complete circuit. The electric current from the welding machine will flow smoothly if there is less resistance in the circuit. If your gun is already stuttering and sputtering, don’t just let it be. Also, bad ground increases the chance of the machine to spark and shock. Find a good ground with clean metal as close to the arc as possible to improve your welding quality.
Choose the right gas
The welding process and output would have a big improvement if the right gas is used. You have to consider the type of material being welded if deep penetration is needed, and how important the weld appearance is. Then, use the right gas for the specific project. Doing so would protect the weld pool from exposure, make your arc more stable, and improve the quality of the weld deposit.
Use both hands
Use both hands to handle the welding apparatus, especially when MIG welding. This would make your handling more stable and help you control your speed better. If you’re MIG welding. Rest the crook of the neck on one hand while the other hand is on the trigger. Don’t forget to use heavy welding gloves to avoid injuries.
Pace yourself
The speed of welding affects the output greatly. There are times when a welder becomes too eager and pushes the arc too quickly along the joint. It results in a thin and tall weld that doesn’t penetrate deep enough. Slow down and weld at just the right pace.
Listen
If you’re an inexperienced welder, you might not think of using your ears to make a fine weld. Listening to your work is a great way to ensure that its quality would be good. A steady buzz while welding is what you would want to hear. If you hear a steady hiss, then the voltage might be too high. On the other hand, a loud, raspy voice would mean the voltage is too low.
Match all your equipment
When MIG welding, you need to match your equipment properly. Have you ever found yourself constantly changing the feed speed, but never getting it right? Maybe the wire size didn’t match the drive rolls, gun cable liner, and contact tip. If the rolls are too large, your weld quality will be affected. Double-check your equipment before starting the process.
Use the proper method
You can either push and pull along a joint when welding. The most common method is by pushing it towards the direction of the weld, or the forehand method. This produces a flat, wide, and smooth surface, and it doesn’t penetrate as deep. This is best for joints where appearance matters.
When you pull or use the backhand method, the penetration would be deeper and the weld would come out narrow and tall in the center. The method to choose depends on the project itself. How deep do you need to penetrate the material? How thick is the metal?
Pay attention to your bead
Your welding bead can tell you much about how the welding process went. If there were mistakes made, then it would reflect on the bead itself. Look at the finished bead and try to observe. Is there anything wrong with it?
For example, if the bad is ropy or convex-shaped, then your setting was too cold for the thickness of the metal and it wasn’t enough to penetrate to the base. If it’s concave-shaped, then there is a problem with your heating input.
Key Takeaway
No matter how experienced a welder you may be, there is always room for improvement, and mistakes can still be made. By taking note of the ways to improve welding quality in this article, your work might change for the better. Ensure that your welding output is flawless and any project will become a success.
If you’re welding materials, then you’re surely working with metal. Metal Exponents is the finest steel importer and supplier in the Philippines. We’ve been doing this for more than 40 years, so any of your metal needs, we have! Take a look at our products here and get in touch through this link!