5 Common Issues with Laser Cutting and How to Avoid Them
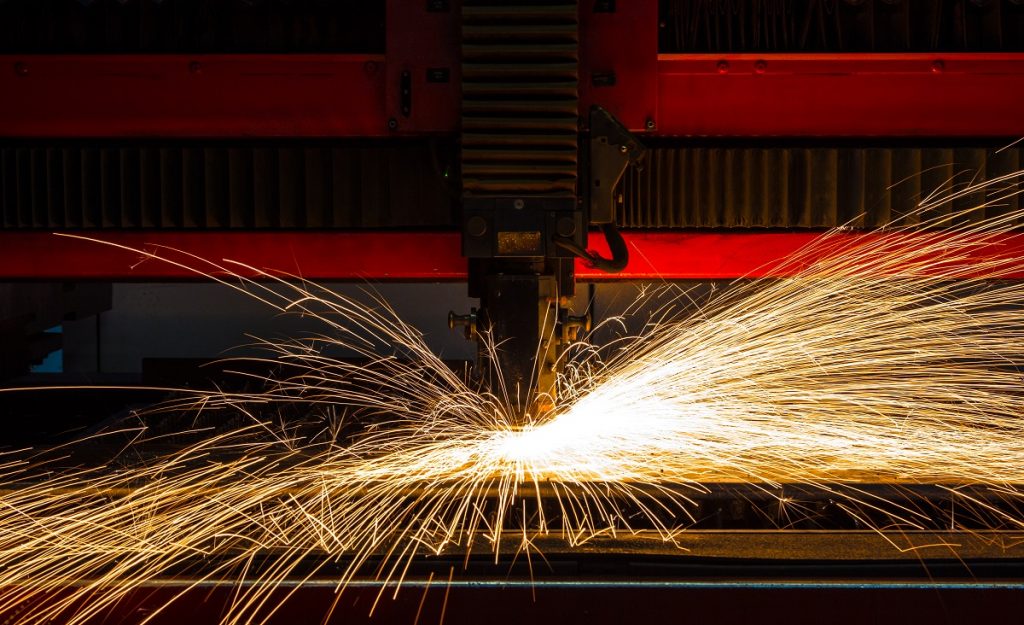
What are some common issues with laser cutting?
- Issues with cutting thick metals
- Uneven cutting
- Presence of burrs
- Deformations with small holes
- Insufficient cutting depth
The term “laser cutting” is relatively straightforward as it refers to a process that uses a laser to make cuts or incisions on different materials. For the metal fabrication industry, laser cutting can be applied on different metals or alloys, such as zinc, carbon steel, aluminum, cutting steel, or tool steel. Avoiding common issues with laser cutting is what makes it possible to produce metals with consistent shapes and sizes. However, this may not totally be achievable, which is why manufacturers implement other post-processing and secondary techniques to offset these challenges.
Typical defects in laser cutting can be affected by several factors, such as quality of cutting equipment, choice of material, operator expertise, and many more. Issues that can take place can be anywhere from the typical uneven cut, to deformations caused by material sensitivity and combustion.
As laser cutting continues to be one of the most reliable forms of product manufacturing, many industries rely on companies that offer this type of service for high tolerances. Likewise, laser cutting service providers have to constantly keep an eye out for these issues to sustain client demand. Read on to learn more.
Issues with Cutting Thick Metals
Any manufacturing firm understands that thicker materials are generally harder to cut than thinner ones. This is one specific issue for laser cutting of carbon steel, especially if the plate has a thickness of more than 0.4 inches. Many limitations when it comes to laser cutting depend on a number of factors, such as heat conductivity, laser focus, surface reflection, type of metal/alloy, part geometry, and many more. When a machine has to cut far thicker metals, it could increase the chances of thermal runaway or blowout onto the material.
This type of issue can be resolved by focusing the beam and reducing the spot size. This makes the laser cutter a much sharper and more effective tool capable of cutting a variety of metal thicknesses. For improved performance, laser cutting may also be accompanied by gas-assisted technology where the focused assist gas helps prevent combustion and remove debris and molten metal from the kerf (material that has burned away).
Uneven Cutting
As mentioned before, part geometry is crucial in any successful laser cutting operation. With this in mind, different part geometries can influence the quality of cutting done on the metal.
When cutting small corners or areas, understand that these will absorb more heat, making it more challenging to achieve consistent cutting speeds. The same is also true with uniquely shaped metals that have complex part geometry. As is the issue with cutting metals, uneven cuts also influence thermal runways or blowout increases.
The most effective way to limit instances of uneven cutting is to focus or speed up a laser when cutting curves, angles, and other complex formations. This helps reduce deteriorated edge quality and blowout. Another option for customers is to choose a simplified metal design that doesn’t have too many angles or corners. Not only does this speed up the laser cutting process, but it also makes the process more cost-effective by reducing expenses on fixing defects and changing materials.
Presence of Burrs
A burr is simply a rough edge or uneven ridges that may inevitably take place during laser cutting. When left unaddressed, this could have functional consequences on the finished part, as the burrs lead to reduced safety during handling and storage. The same is true when the burred metal is in use under extreme conditions — the sheet will gather increased stress levels, which speeds up wear and tear and damage formation.
Laser cutting equipment operators see to it that they determine the focal point of the machinery before they start with the operation. They also have to restart the machine, speed up the cutting speed, and adjust the output value in order to reduce instabilities that lead to the burrs.
Deformations with Small Holes
Forming small holes on any metal through laser cutting can be a challenge due to the small surface area to work with. Small diameters and part thickness affect hole deformations. This is why small cuts lead to high energy concentration until the material is eventually charred.
This is why whenever there’s a need to punch holes in the metal, operators turn towards a more stable laser cutting method known as soft puncture (also known as pulse perforation). This not only leads to consistent hole shapes but a smooth finish on the surface of the metal.
As opposed to continuously focusing the laser cutter on a portion of the metal, pulse perforation involves applying the laser in a pulsating or intermittent fashion that makes the positioning more accurate. This effectively prevents the charring of the surrounding material and ensures that no working residue is left after the completion of the cutting cycle.
Insufficient Cutting Depth
Inadequate depth when it comes to cutting or engraving a metal workpiece is usually caused by errors in the focal point adjustment. When the laser is not properly directed onto the material, this heavily affects the cut quality, resulting in uneven areas where uniformity is expected.
The solution to this is to adjust the depth, output power, or slow down the speed of the engraving. However, in cases where these have already been done without a clear change in the quality of the laser cut, the operator should check the equipment for worn-out components such as the laser tube or the power supply itself.
Key Takeaway
Many of the common issues with laser cutting are a direct result of adjustment concerns with the machinery itself. To reiterate, a lack of focal point focus for the laser leads to issues like insufficient cutting depth, burrs, uneven edges, charred corners, and many more.
Metal fabrication or manufacturing firms understand how critical it is to assess laser cutting equipment and optimize their processes to avoid such defects from happening in the first place. Nevertheless, laser cutting continues to be useful for many industries that need meticulously cut parts that meet tolerances.