What Are the Benefits of Aluminum Sheet Metal Fabrication?
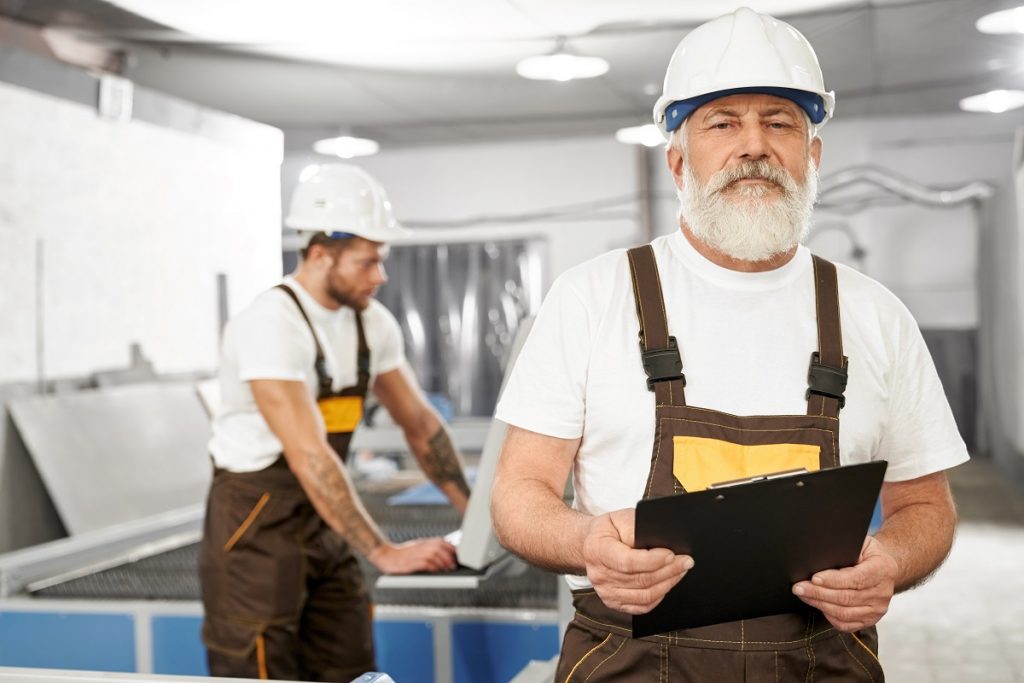
What are the benefits of aluminum sheet metal fabrication?
- Lightweight
- Durable
- Versatile
- Cost-effective
- Environmentally-friendly
- High heat tolerance
The benefits of aluminum sheet metal fabrication are unmatched when it comes to manufacturing. Compared to other materials, aluminum has a number of advantages — it is versatile, eco-friendly, durable, and non-combustible. This makes aluminum the prime choice when producing different types of custom-made metal parts for final distribution or assembly.
Currently, there are a number of common materials used by fabrication companies to come up with quality products at reasonable price points. Some of these include stainless steel, steel, and even plastic.
But whenever strength-weight ratios and cost are concerned, it’s clear that aluminum stands out from the rest of the pack. Its material properties make it one of the lightest materials for fabrication, without sacrificing toughness. If you’re in need of fabrication services, then choosing aluminum is one of the best choices that you’ll make for your bottom line.
Lightweight
As mentioned, one prime advantage of aluminum over plastic or steel for that matter is the weight-strength considerations. While plastic is significantly lighter — ABS plastic, in particular, has a density of 1.08 grams per cubic centimeter — aluminum fares better in high impact conditions because of its build. On the other hand, steel parts may be favored because of their strength, but they may be inconvenient in weight-reduction situations.
As a perfect balance between these two varying material choices, aluminum continues to be reliable wherever lightweight-ness and strength are concerned. It may not be as light as plastic, but its metallurgical values are much better. This makes the use of aluminum-fabricated parts popular in such industries as automotive manufacturing, construction, furniture-making, and many more.
Durable
Aside from its weight advantage, aluminum is also a durable material — even competing in the same field as steel, stainless steel, polymers, and timber. One of its most well-known and distinctive features is non-corrosiveness. Because these alloys contain no iron, the material is almost impervious to rusting and other types of material destruction.
Without any use of coatings or surface protection, mill-finished aluminum parts fare particularly better than other materials in outdoor environments. For example, an aluminum-alloy outdoor table will last for much longer decades without showing any signs of deterioration. Compare this to non-galvanized or non-coated steel which is not only denser but is also prone to corrosion.
The aluminum oxide formed on the surface of the aluminum, adds a natural layer on the metal’s surface, effectively protecting it and making it last for several decades. Whereas steel would have to be coated through galvanizing or plastic coating for added maintenance.
Versatile
In metal fabrication, ductility is defined as the ability of a material to be altered, shaped, or changed into forms — such as being drawn into a coil, wire, or thread — without showing cracks or any other deformity. Aluminum fits this property exceptionally well because it’s also ductile and machinable. As fabrication depends on cutting, punching, shearing, stamping, and other manufacturing processes, companies will have no problem incorporating a versatile material like aluminum into their processes.
From your perspective, versatility in metal fabrication allows you to come up with a wide variety of shapes and designs. Working with aluminum becomes much more convenient than steel because the former is easier to cut. You can come up with a range of complex and simple designs with aluminum, and still meet your budget requirements.
Cost-Effective
Whenever you require the services of a metal fabricator, the cost is a critical factor in your decision. As much as you want to prioritize high tolerances and complex fabricating techniques for your product, you will need to also assess its final cost resulting from material choice, labor, design complexity, and the like.
When you’re prioritizing cost-effective solutions, aluminum is an ideal option. As mentioned before, prefinished aluminum parts don’t require complex machinery to draw into wires, bend, or cut into different shapes. This makes the lead time for aluminum fabrication much shorter, unlike steel which requires more tools and methods to simply cut into the desired shape.
Environmentally Friendly
The metal fabrication industry continues to adopt solutions in order to consistently meet customer demand. One of these is the demand for environmentally-friendly fabricating solutions through better waste production outcomes, higher energy efficiency, and improved recyclability of parts.
Although the metal industry, in general, is energy-intensive, it continues to make up for it by adopting more sustainable approaches. Choosing aluminum is one of these, as it is an incredibly eco-friendly raw material choice.
Much of the aluminum in use today come from recycled and refined scrap materials produced in the last 10 decades or so. Scrap aluminum can be infinitely recycled without a compromise on its original properties and advantages.
High Heat Tolerance
Steel may be better when subject to extreme temperature conditions, but it’s not necessarily the most economical choice for fabrication. This makes aluminum a formidable alternative because of its cost-efficiency compared to aluminum, and heat tolerance in comparison with plastic.
Aluminum parts hold up well in applications where heat and combustion rates are considered. Some examples include car manufacturing, medicine & healthcare, petrochemical industry, construction — you name it. It is non-combustible, does not easily melt, and will last for several years while still being strong, flexible, versatile, and easily machined.
Key Takeaway
Discussed in this short guide are just some of the many benefits of aluminum sheet metal fabrication for industries and clients. Over the years, aluminum as a material has been widely used as a cost-effective and durable alternative to steel, wood, and plastic. In metal fabrication where cost and high-tolerances are two primary concerns, aluminum has shown itself to be an excellent material that addresses these gaps.
The next time you’re in need of sheet metal fabricated parts, make the switch to aluminum. It’s capable of meeting your design requirements while successfully balancing out considerations on cost, weight, and material longevity.