Metal Stamping Vs Laser Cutting: Which is Better?
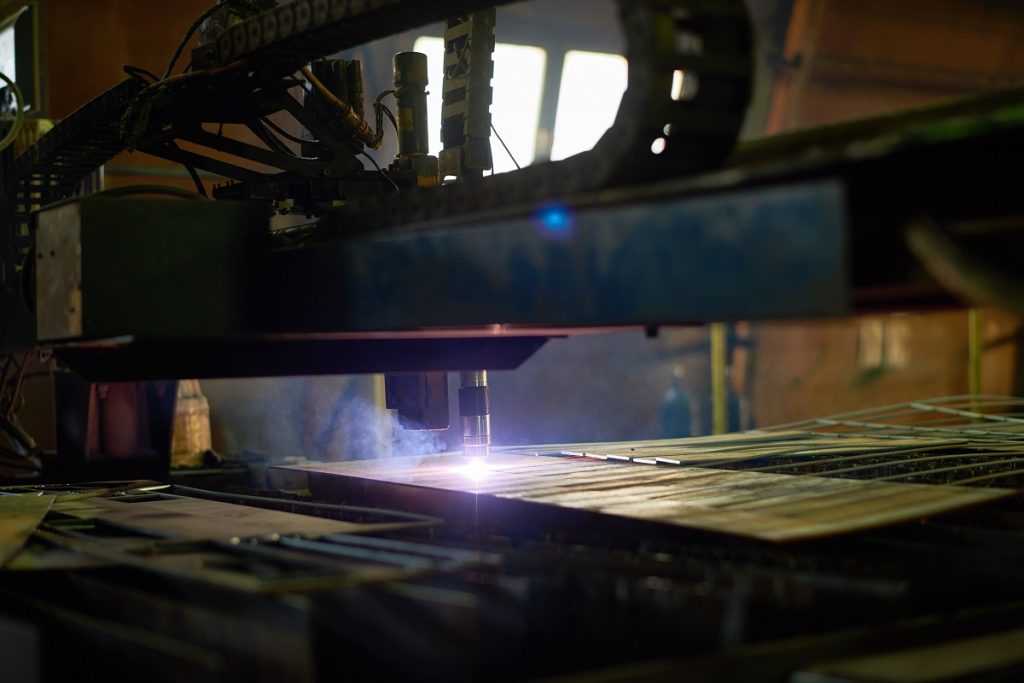
What are the differences between metal stamping vs laser cutting?
- Process
- Cost
- Time
- Capabilities
There are many ways to create custom sheet metal forms, two of the most popular methods using either metal stamping or laser cutting machines. These machines are used to create custom metal products for all sorts of purposes. Those looking to use either method might ask: “What are the differences between metal stamping vs laser cutting?” when considering which method might be better for their product. The answer depends on many factors, which this article will discuss. Read on to learn more about the benefits and drawbacks of these two processes.
Process
The first way to differentiate the two is to describe the processes each will undergo to make your metal components. Metal stamping makes use of a die pressed into the metal with enough force to shape the metal. This die is used as a mold for the desired shape. Based on your designs and specifications, it is very likely that this die will be custom-made for your project, which can then be used repeatedly to make the number of desired parts.
For this method, the material used must be malleable enough to mold to the die when pressed down, to avoid putting the die through too much pressure. If the metal is not malleable enough, this could prematurely damage the die and add additional costs in replacements.
Laser cutting uses a powerful and precise laser to get the job done. This laser is made of an energy emission device that puts out high concentrations of photon streams. This is directed at the material and can be guided through a pre-programmed path to make the desired shapes in your material. Because they can be computer programmed, the cuts are accurate and the result is a smooth and polished edge with a quality finish.
Cost
Cost is always one of the first things that are discussed when considering different methods in creating your products, and when it comes to metal fabrication it is important to not only consider the cost of raw materials but also the costs of machinery and manpower needed to process those materials. When it comes to metal stamping vs laser cutting, the biggest issue is the amount of money it takes to set up the machines and get the initial units produced.
Metal stamping can cut some of the additional costs that come from needing more manpower and machines for operation as it can combine multiple operations in the same process. Machine stamping has the capability of performing operations such as tapping, extruding, fastening, and more. There are many opportunities to combine these additional steps in a stamping press stroke, which can reduce the part costs. This can also offset the initial investments you will make in using these stamping machines and tools.
Laser cutting is also able to cut costs, just in different ways. While it can cost more to purchase laser cutting machines for your operations, it is also a highly automated process. A majority of the steps in this process can be facilitated with the use of computers, which greatly reduces labor costs when compared to hand-operated machinery (such as those used in metal stamping). Furthermore, because lasers do not get worn down like traditional machines, there is little worry about replacement costs. In fact, bigger orders could make your laser cutting more cost-efficient in the long run.
Time
Time is also something to be considered when examining the benefits and drawbacks of these two methods. Manufacturing time is another thing that affects your overall expenses in the long run. The faster you can finish manufacturing your parts, the less you’ll end up spending on the machines, materials, and labor needed for the production process.
Metal stamping jobs require the creation of a custom die that can only be used for the production of a particular part. The creation of the die creates a much higher upfront cost, however once created, the die can be used repeatedly to make a large number of parts. The equipment needed for machine stamping takes much longer to be readied than the equipment for a laser cutting process. However, the time needed to produce each part once the system has been readied can take less time overall.
One of the biggest parts of using the metal stamping process is the die, which is used to mold your metal materials. The creation of the die takes time and costs a lot of money. Additionally, that die can only be used in the fabrication of a specific part. If your product needs multiple parts, it will need multiple dies to be manufactured. Another aspect of this method that can add time to the overall process is the quality of the die. If there is an error in the die, it creates a permanent defect in any metal that was processed by the metal stamping machine using that die. Dies also need to be replaced over time, which is more likely depending on if there is a large volume of parts being fabricated in a short period.
However, once the dies have been made, they can be used repeatedly to make a large number of the same parts. It can process a higher volume of metal and produce a greater number of parts in a shorter period than laser cutting can.
When it comes to laser cutting, the setup is done digitally, which means productions can start much earlier than with metal stamping. No additional tooling is required for laser cutting to work as it only relies on whatever program is being fed into the machine. Additionally, each part is created individually, so an error in one piece does not mean the whole batch needs to be inspected and replaced with a new one. In general, laser cutting may be the better option for short to medium production runs, especially if the project is running on a tight schedule.
Capabilities
The complexity of the parts is also a factor to be considered when weighing the two methods. The capabilities of both methods vary, and when choosing the appropriate option, you have to consider whether the machine will be able to create the desired design of your product.
With metal stamping machines, they can do more than just press metal into shapes. They can cut holes, swage, or coin metal into specific shapes to fit your product needs. They are also able to shape and cut metal that is thicker than what laser cutting machines can manage. Metals with higher temperature resistance can also be hard to process using laser cutting machines due to their high melting points, however, metal stamping can process these with ease and this makes them the preferred choice for these metals.
With laser cutting machines, they are more suitable for parts that have complex forms of geometry. This is because there is no physical tooling or handling required during the process, which allows for more intricate, machine-guided cuts to be made into the metal. Laser cutters can also enable manufacturers to nest parts of different shapes and sizes onto the same sheet, which is ideal for products with multiple parts. Another capability of laser cutting machines is that it finishes parts with smooth edges, which in turn reduces the risk of burrs or rough metal objects. This ends up with a reduced need for secondary operations needed for the smoothing and finishing that is common for most metal products.
Key Takeaway
When considering metal stamping vs laser cutting, it is advisable to read about the process and what each entails in costs, time, and capabilities. Both methods are used by thousands of manufacturing industries, and while both can perform the same tasks, they come with their benefits and drawbacks. This is why it is important to opt for the method that best suits your needs and budget.