Robotic Welding Vs Manual Welding: The Key Differences
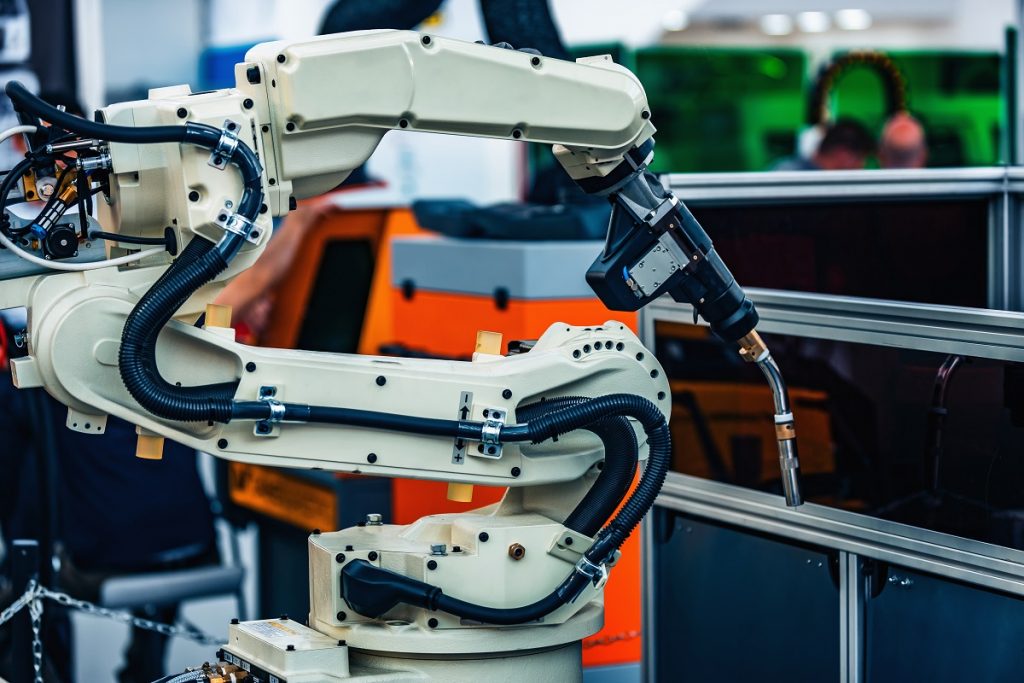
What are the differences between robotic welding vs manual welding?
- Weld Quality
- Welding Speed
- Flexibility
- Risks
- Costs
Every now and then, a major innovation comes along and changes how a certain job is done. In metal fabrication, applying robotics to welding has improved output greatly and created advantages that manual welding doesn’t have. Despite that, manual welding remains popular as there are things that robots can’t do. Here, we’ll take a look at the key differences between robotic welding vs manual welding to figure out which option is better. Consider these factors when deciding what type of welding you need for your fabrication project.
Weld Quality
The quality of the weld depends on the accuracy, skill, and experience of the welder. When robotics comes along, everything becomes precise. Weld quality means the accuracy, precision, strength, and appearance of the final output.
Robotic Welding: Because of advanced robotics, electronic process controllers, and computer processing, the weld integrity of robotic welding surpasses what manual welding can do. The movements of the robot are always carefully calculated, making each weld highly accurate. Moreover, the quality of output is consistent throughout all projects, sans any complications.
Manual Welding: Machines are generally more accurate than humans, no matter how experienced the welder may be. Manual welding is also prone to human error, making its work inconsistent. The edge that manual welding has is that human welders will be more aware of errors during the process. Robots won’t be able to correct that until the process is over, but humans will recognize it quickly and troubleshoot.
Welding Efficiency
For some large-scale projects, speed is almost as important as quality. Producing large amounts of output needs efficient work. If this is the type of project you have, you would want something that works quickly but doesn’t sacrifice quality.
Robotic Welding: As you would expect, machines work faster than humans. Robotic welding yields greater output than manual welding while still being consistent with quality. A huge factor here is that robots don’t get tired and never lose focus, and they can work for 24 hours straight if needed. Meanwhile, humans only have limited endurance and focus.
Manual Welding: Human welders are less efficient than machines in many aspects. The major difference is that you can replace manual welders easily to avoid setbacks in the production process. If a human can’t work, they can be replaced by another equally skilled worker. If a machine malfunctions, it will take some time before it can be used again.
Flexibility
The processes of metal fabrication are not the same for every project and every material. If you’re working with metals of different specifications, flexibility is a desirable characteristic.
Robotic Welding: Robotic welding excels in producing at high rates for repeatable tasks, but the machines are not as flexible as manual welders. Changing projects would mean some additional reconfiguration for the machines, which also adds to the costs.
Manual Welding: Professional welders, especially those with more experience, can go into various projects right away. No time or resources would have to be used for retraining or reconfiguration.
Risks
Risks are a part of every project, so it’s important to know about them before committing to something. It’s always best to keep risks at a minimum, so when it comes to welding, think carefully about your choice.
Robotic Welding: The main risk for robotic welding is a malfunction. If a machine breaks down, the processes stop and it would need to be repaired. The situation would be worse if you’re relying solely on the machine that malfunctioned. It could cause additional costs and slow production.
Manual Welding: Humans are not like machines that can easily be repaired and can’t get hurt. If a manual welder is injured, it can be a very serious matter.
Costs
When you’re deciding whether to use robotic welders or hire manual welders for a metal fabrication project, you have to be aware of the costs. There are potential costs and the expenses that you need to get the welders in the first place. Here are the differences:
Robotic Welding: With robotic welding, labor costs are reduced. You wouldn’t need to hire specially trained professional welders, only more available machine operators. However, the cost of the machine itself is larger, and any subsequent malfunctions or part replacements would add to the amount you need to spend.
Manual Welding: Professional welders need to be paid a proper wage that will be subtracted from your budget in the long term. The advantage is that you would not need to shell out a large amount of money off the bat, like how you would with robotic welding. Be aware that if a worker is injured on the job, you may also have to shoulder the medical expenses.
Key Takeaway
The key differences between robotic welding vs manual welding show that each method can work better than the other in specific instances. The quality, efficiency, flexibility, risks, and costs should all be factored in before making a final decision of what to invest in for your fabrication project.
No matter which welding method you invest in, you would need the finest steel products for metal fabrication. Here at Metal Exponents, we offer reliable, high-quality metal products at competitive rates. Take a look at our products here, and send us a message for your inquiries.